超低硫管线钢的生产及脱硫参数分析
发布时间:2009-11-02 作者:余健,李晶
对于大多数钢种来说硫是有害元素,硫元素 降低钢材的韧性和强度,增加钢材的热脆性和锈 蚀性[ 1 ] 。随着对钢品质的要求日益提高,低硫钢 受到广泛关注。例如965 MPa 高强度钢硫质量 分数从80 ×10 - 6 降到20 ×10 - 6 ,层状开裂减少; 大口径高强度管道钢降低硫质量分数到(20~30) ×10 - 6 可保证韧性和抗SSCC(硫化物应力腐蚀) 性能;降低硫质量分数到30 ×10 - 6 ,汽车轮箍火 花焊接成形缺陷也会降低50 %~90 %[ 1 ] 。HIC (氢致裂纹) 和SSCC 对管线的破坏力巨大,而管 线钢中的硫是诱发HIC 和SSCC 的重要元素,控 制钢中硫含量成为管线钢冶炼的重要任务。本文 利用精炼炉渣脱硫模型对工业脱硫试验中主要脱 硫参数进行了分析。
1 试验方法及结果
1. 1 试验方法
文献[ 2 ]指出了生产超低硫钢对冶炼各工位 提出的硫含量控制要求。试验确定了各工位的控 制要求:铁水预处理后w (S) ≤30 ×10 - 6 ;转炉出 钢w (S) ≤50 ×10 - 6 ;L F 后w (S) ≤20 ×10 - 6 ;VD 后w (S) ≤10 ×10 - 6 。
试验工艺流程为:铁水预处理→150 t BOF → 150 t L F →150 t VD →CC。基本操作要求如表1所示。按各工位硫含量控制要求和表1 设定的精 炼操作方法冶炼8 炉低硫钢,并分析了炉渣特性 对脱硫的影响。
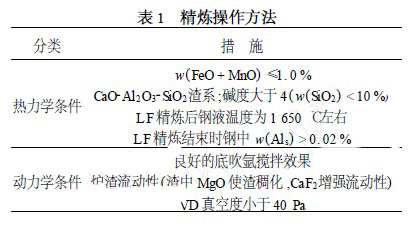
对精炼过程系统取样,包括L F 前、L F 后和 VD 后钢样,L F 后和VD 后渣样。检测钢样中酸 溶铝含量、硫含量和渣样成分。
1. 2 试验结果
硫含量检测结果如表2 所示,由表2 可知, L F 精炼前钢中硫质量分数均在50 ×10 - 6 内,L F 精炼后钢中硫质量分数控制在20 ×10 - 6 内,VD 精炼后钢中硫质量分数达到超低硫水平在10 × 10 - 6 内,第3 炉和第8 炉达到极低硫水平,硫质量 分数为5 ×10 - 6 。表3 为L F 精炼终点渣成分。
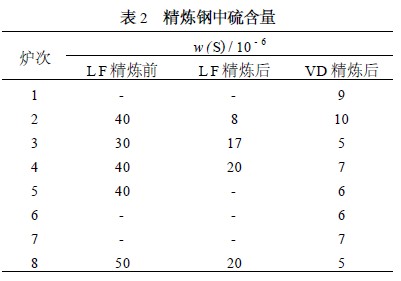
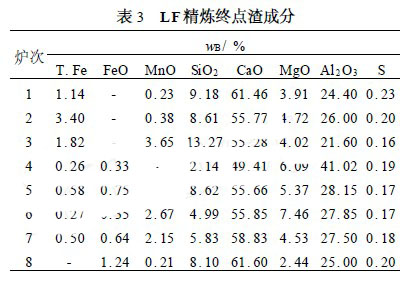
2 讨论及分析
2. 1 精炼脱硫模型计算分析
为了分析炉渣特性对实际脱硫效果的影响,运用脱硫计算模型[ 3 ] 计算了脱硫参数,各脱硫参 数如表4 所示。
表4 表明:试验炉次的炉渣光学碱度为0 . 81 ~0. 85 ,与文献[ 6 ]中的观点“渣系的光学碱度Λ 为0. 81~0. 83时,脱硫能力最强”基本符合,此时 渣硫容量的范围在0. 028~0 . 040 。
理论计算的硫分配比远高于实际硫分配比, 应考虑使实际硫分配比接近理论脱硫分配比,脱 硫反应的限制性环节为钢水侧或炉渣侧的传质速 度[ 2 ] ,因此在不裸露钢液的情况下,加强L F 底吹 强度,能有效提高脱硫率。
2. 2 主要参数对脱硫的影响分析
2. 2. 1 碱度对脱硫的影响分析
试验炉次L F 精炼后炉渣碱度与硫质量分数 的关系如图1 所示。