用于冷轧机的自适应调整模型
发布时间:2009-07-30 来源:ABB评论
提高产品质量主要集中于寻找一 些方法,来降低厚度和平直度 公差,提高表面的质量。另外,必 须增加轧机灵活性,满足对产品品 种日益增长的需求,同时,高生产 率 (产量和生产能力) 是在全球经济 中保持竞争力的一个先决条件。 从自动化角度来看,这些需求可通 过下列具体要求实现:
■可靠和现代化的自动控制系统
■可靠的传感器和执行机构
■自适应调整模型用于编制轧制表1) 和预设定计算■先进的技术控制解决方案
■直观可视化、运行与诊断系统和 概念
为实现上述目标,使用了数学模型 来计算轧制表和轧机的预设定计算 (见图 1 )。根据卷材和轧辊数据, 轧制表使用压下量和张力表预测工 艺过程,压下量和张力表来自经验 和数学分模型。模型主要由四部分 组成:材料的加工硬化曲线 (流动应 力模型)、辊缝摩擦模型、辊缝模型 (提供轧制载荷、驱动扭矩、前滑 和卷材温度) 以及轧机模型 (提供卷 材平直度执行机构和辊隙位置参照 数据)。
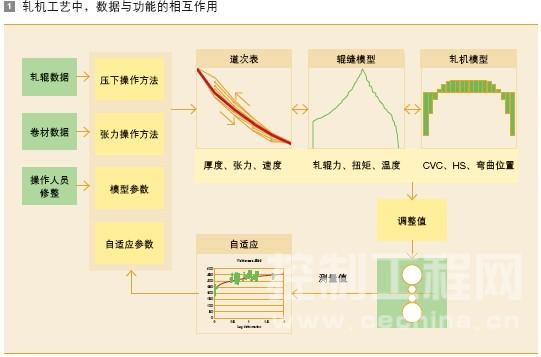
在每个轧制道次过程中,收集并筛 选测量值,与相应的预测值进行对 比。然后计算出自适应参数,使预 测值与测量值一致。
轧制模型由一套分模型组成, 分 模型紧密相连,主要以物理原理为 根据。
主要分模型如下:
■轧制表安排 (计算道次数以及相关 卷材厚度分配)
■预设定 (计算所有必须的预设值)
■自适应模型 (通过测量改变模型) 每个卷材都会生成调整和适应报 告,并报告储存于数据库内,用于 进一步分析和离线微调模型。
轧制表计算
轧制表计算的任务根据给定的卷材 数据 (材料等级、带材宽度、起始和 最终厚度) 确定各个道次合适的压下 量。首先,从初始厚度开始正向计 算每个道次的最大压下量,然后, 再从最终厚度反向计算每个道次的 最大压下量,确定最佳道次所在的 边界条件 (见图 2 )。然后,考虑到轧 机和常规操作极限所决定情况的边 界条件,努力找出接近所选标准的 压下路径,这是实现轧制时间最小 化的简单办法;或者让所有道次都 承受同样的轧机载荷,每个道次的 轧制时间可以简单地达到最小化。 上述标准操作极限系指根据产品分 组在表中确定的工艺过程边界条 件,它规定诸如第一道次和最后一 个道次的最大压下量、卷取张力等 参数。
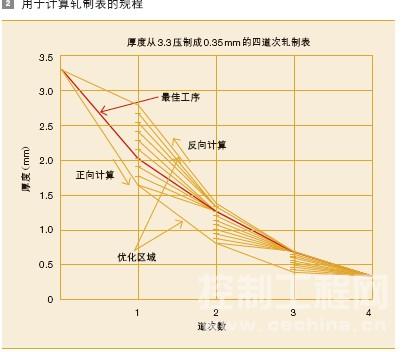
每个道次的压下量可根据几项标准 优化处理。与通过量或带材质量 (如 平直度和板材表面) 相关的标准有时 相互矛盾。轧制表的编制可以满足 压下量和压力限制的要求,也可满 足压下量和力量趋势 (如每道次恒 定压下量或每个道次减少轧辊压力 等) 的要求。可以优化轧制表,平衡 所有道次或机架所需的电机功率以 获得最大轧制速度。改变压下量或 张力分配,就可达到这样的目的。 为了满足运行要求,如从轧机某侧 装料和卸料,可执行奇数或偶数轧 制道次数。也可在最终轧制道次配 置固定压下量。在一个道次轧制过 程中,比如中间厚度没有达到要求 或材料硬度比预计高时,可以重新 进行计算,修正后续道次的参数。 轧制表计算中的关键要素是以物理 定律为基础的辊缝模型。除了进口和出口厚度以及张力外,此模型还 要求将材料的变形抗力以及轧辊和 卷材之间的摩擦特性作为进口数 据。变形抗力以流动应力曲线的形 式描述,以每个轧制阶段对材料试 样进行的拉伸试验作为根据。轧 辊粗糙度和轧制速度是影响轧辊 咬入摩擦状况的重大因素。摩擦 变化对轧制载荷的影响可从低碳 钢和轻型钢材上比较清楚地看到 (见图 3 )。
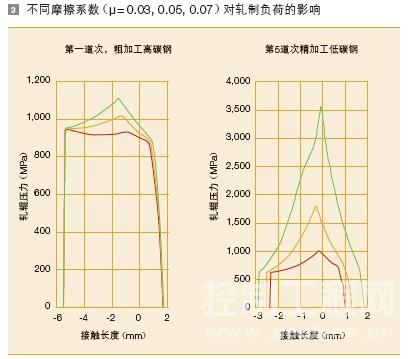
预设模型
在一个轧制表确定之后,预设工序 将计算出剩余的调整数值。有时, 工序数据 (如厚度、张力) 从轧制表 中查找或由外部系统提供 ( PPS, ERP, Level 3 )。
用于预设计算与卷材相关的必须包 括的输入数据是:
■进口厚度、宽度、进口温度
■热轧厚度或上次退火厚度
■材料等级、退火类型
■卷材侧面,卷材外径
■出口目标厚度 (开坯机) 或出口目 标延伸量 (平整轧机)轧辊直径、凸度、锥度、长度和材 质等轧辊实际数据对于精确计算也 十分重要。
轧机和传动限制、标准操作规程、 适应系数、屈服应力和摩擦力等一 般性参数存储于当地的 2 级 MES系统 内。不同分模型之间密切相连 (见图 4 ),一种模型的输出可作为其他模 型的输入。
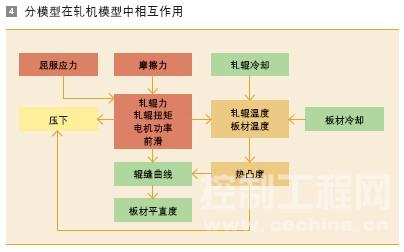
预设计算功能产生喂料、轧制和卸 料状态等所有道次必须的调整值。 计算数值反馈给 1 级层次上的不同控 制功能。传输的主要预设数值列于 资料库2 中。
当满足下列条件时,轧制表 和预设计算自动被激活:
■首次获得卷材数据 (可信 性检查)
■ 卷材进入“下一卷”状 态或当下一卷安装于开 卷机上
■ 前一卷的自适应过程已 经完成
■操作工人手动请求 操作人员可以看到计算获得的预设 值,当操作人员对修正值进行必要 修改并进行最终检查后,即可将预 设值传送到第一级层次,卷材喂料 随即开始。卷材状态从“下一卷”变成“当前卷”。只有当轧机停止 时,用于那卷的预设值才能改变。 操作人员可看到当前卷材的整定 值,并准备下一卷的设定值。
不同分模型密切相连,一种 模型的输出可作为其他模型的 输入。
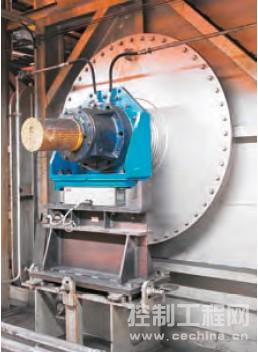
主要预设模型的组成部分
轧制模型使用几个分模型作为组成 部分:
张力模型
张力模型根据具体张力而确定,这 些张力根据卷材厚度和材料屈服应 力以及张力操作规程计算出来。特 别是,第一个开卷机和最后卷的取 张力取决于冷轧卷材的预处理和后 处理。采用不适当张力进行轧制会造成卷材滑移、不稳定轧 制和退火过程中发生黏结等 现象。
当张力可能超过卷取机和开 卷机最大数值时,必须进行 限制。使用辊式张紧装置 时,开卷机与进口张力以及 出口与卷取机张力之间的比 例也会受到限制。
速度模型
最大轧制速度受下列因素制约:
■传动最大功率 (轧机传动、开卷机
或卷取机传动)
■齿轮箱速比容许的最大传动速度
■轧材最高出口温度
■与质量相关的速度限制
速度模型降低速度直至满足这些制 约值的要求。
辊缝模型
辊缝模型又细分成开坯机和整平 机模型, 回火轧机和箔材轧机模 型等。
当压下量超过百分之五以及平均厚 度和接触长度比例较大时,辊缝以 福特、埃利斯和布兰德的经典圆弧 形理论为根据,这种方法考虑了辊缝中卷材的塑性和弹性变形。变形轧 辊半径根据希契科克方程式计算。 对于整平和箔材轧制配置 (压下量以 及平均厚度和接触长度比都较小), 采用根据弗莱克和约翰森的理论建 立的非圆弧模型进行在线调整,模 型计算轧辊力量和扭矩、前滑、变 形和摩擦能量等。它使用屈服应力 和摩擦模型,工艺扰动用自适应系 数进行补偿。
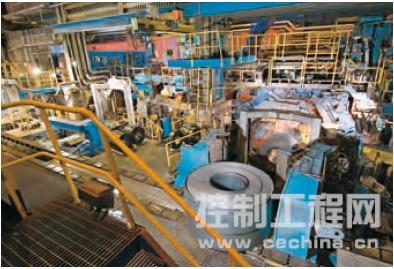
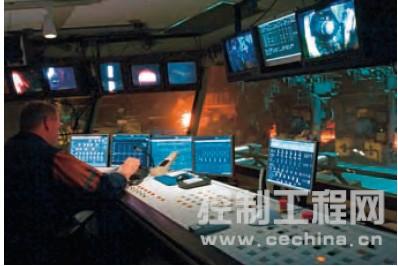
给定产品的屈服应力根据变形、变 形率和卷材温度进行计算。产品可 用诸如材料分组、材料等级或预处 理 (如退火类型) 等多种性能进行确 定。与材料等级相关的参数需要与 用户密切合作确定。
采用不适当张力进行轧制会造 成卷材滑移、不稳定轧制和退 火过程中发生黏结等现象。 摩擦系数根据工作辊的粗糙度、材 质、速度和道次数量进行计算。
带材温度模型
带材温度模型旨在预测带材在轧制 过程中所有阶段的温度状况。带材 温度用于屈服应力模型和轧制表 的计算。影响带材温度的因素包括带材的进口温度、空气冷却、冷却 池的吸热、辊缝中的热量产生以及 与工作辊的热交换等。
如果有单独的带材冷却方式,则需 要计算带材冷却液流量,使出口带 材温度保持在确定的最高温度之 下,以免由于冷却过程中带材温度 过高, 在带材表面出现纸印缺陷 (不锈钢) 或点火痕迹 (铝材)。如果 一个道次上的计算冷却温度,在最 大容许冷却油流量的状态下超过安 全极限, 则所有道次的轧制速度 分配均应相应降低。
轧辊温度和热膨胀模型
连续运行的二维瞬态模型可以计算 轧制过程中和轧制之后的工件热 态。使用有限差分技术方法计算工 作辊中的温度分布, 平衡进出轧 辊的热流量。从带材进入轧辊以及 轧辊到冷却液的外部热流量、备 用轧辊和空气等都用适当的热传递 系数表示。然后,根据所产生的温 度分配计算轧辊的立体热膨胀情 况。热输入速率和轧辊上的冷却效 应分布从带材温度和轧辊冷却模型 获得。
平直度模型
平直度模型计算平直度执行机构的 预设值,以便获得理想辊缝轮廓和平直度。有限差分模型考虑进口带材 轮廓、轧辊力、带材宽度、轧辊直 径、磨擦、轧辊的挠度校平和热膨 胀等。
大直径工作辊和小型的冷却效率, 再加上来自辊缝的高热量输入 (如铝 材轧机),有关热量的问题因此尤显 重要。根据轧机类型不同,轮廓模 型可以计算有关工作辊及中间辊的 弯曲力以及轧辊轴向移动定位的预 设值。
连续运行的二维瞬态模型可以 计算轧制过程中和轧制过程后 的工件热态。
辊缝位置模型
敏感度模型
敏感度模型计算工艺过程输入与 输出之间的有限差分。然后,这些 参数可用于计算厚度、张力和平直 度控制的前馈和反馈控制器参数。 这可确保不同产品在所有轧制阶段 都能获得均一质量。
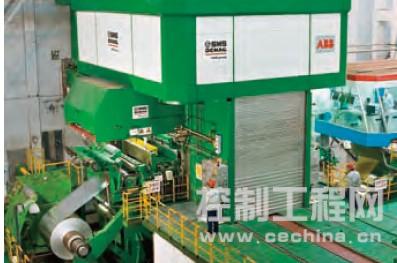
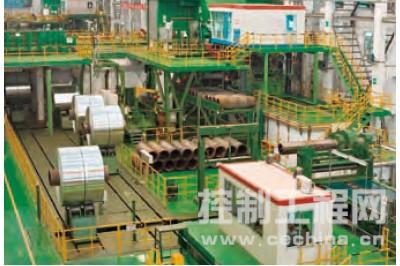
速度前馈参数描述速度和力之间的 相互依赖关系。弯曲前馈参数描述 力与弯曲之间的依赖关系。两种前 馈控制都可以使加速和减速过程中 的扰动减少,是厚度和平直度反馈 控制的重要支撑。
ABB 的预设模型对提高产品质 量和生产率起着重要作用。
自适应模型
建立数学模型时碰到的问题是,虽 然知道工艺过程内的相互关系,但 参数经常未知,甚至会发生变化。 冷轧工艺参数, 如屈服应力、摩 擦、热传递系数等都是未知的,而 且还随时间发生变化。这常常导致 预测不精确。
为了改进预设模型的预测能力,使 用了在线自适应模型, 按照材料 和轧机性能的变化, 更新系数和 参数。
轧制过程中,如果安装有传感器, 可按时间周期中的“输入变量”采 集测量数据 (如进出口带材 厚度、进出口带材张力、 进出口速度、轧制速度、 轧制力、弯曲力、移动和 辊缝位置等) ( 见图 5 ) 。 在进行可信性检查以及对未 测量数值进行筛选和估计之 后,开始重新计算当前卷 材 (图 5 中的“轧制模型”) 和开展不同轧制阶段的自适 应,以便提供自适应系数和 参数,这样,下一卷的调整 计算可用经过改进的准确度 来进行。
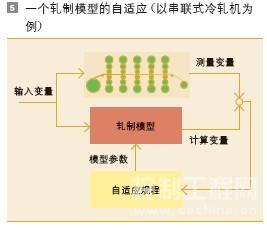
自适应工序从计算和测量变量差中 获得。获取速度可以采用获得增益 进行配置。
短期自适应 (快速获取) 按逐个道 次进行, 而长期自适应 ( 慢速获 取) 在逐个卷材中和一系列类似的 卷材中进行。产品分类的变化 (材 料等级、宽度、厚度等)、轧辊的 变化以及长期停机等因素都要考虑 (见图 6 )。
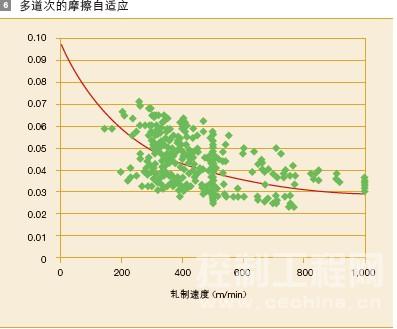
轧机的先进轧辊模型
ABB 的预设模型解决方案对提高产 品质量和生产率起着重要作用。 主要用户优势总结于 资料库3 中。