智能模糊控制轧钢加热炉控制系统设计
发布时间:2009-07-13 作者:潘 炼 王傲能 史 纲
1 引言
轧钢加热炉是冶金企业轧钢生产的主要设备之一。其控制结果的好坏,直接影响到产品的质量。由于炉内被控温度分布不均和某些炉内热工参数难以测量,加上加热炉热容量大,干扰因素多,不易用一般自动控制方式来控制被加热对象的理想温度。特别是炉温控制对杜绝粘钢现象提高加热炉的寿命、降低钢坯烧损提高成材率,节能降耗减少环境污染有重要意义。国内外,在七十年代以前,关于加热炉自动控制的研究工作主要集中在燃烧控制上。如加热炉各主要过程变量的定值控制,炉温与燃料流量的串级控制,燃料与助燃空气的比值控制以及烟道废气的含氧量控制等,也就是处在控制过程基础自动化控制层次上。七十年代后,燃烧控制已经基本成熟,控制研究的重点转移到以追求某种性能指标的优化控制方面,炉内加热过程的数学模型被广泛的应用在计算机控制上。
2 加热炉温控系统分析
轧钢加热炉燃烧控制系统采用计算机控制系统。监控系统基于先进的最佳加热温度控制曲线数据库,采集并计算炉内坯料的实际温度,进行最佳燃烧控制。燃烧控制采用软件控制代替传统的仪表控制系统,实现温度自动控制、煤气/空气的交叉限幅控制。
2.1 燃烧控制系统功能及其结构
燃烧控制系统监控计算机系统,主要完成加热炉最佳燃烧设定控制;由西门子公司的可编程控制器s7-300和操作员工作站mmi及其相应检测执行元件来完成其功能的。系统采用远程输入/输出组件et-200,通过l2-dp数据通信网络来完成数据采集和设备驱动。通过操作员工作站的20几幅画面可对炉内燃烧状况进行监视并进行相应操作。通常c-plc接受来自监控计算机的温度设定值进行温控,亦可直接在mmi上人工设定温度进行控制。助燃风机控制采用西门子simovert-master交直交变频传动控制装置。燃烧控制系统共控制8个燃烧段,每段控制结构基本相同,其结构框图如图1所示。

图1 燃烧控制系统结构图
2.2 燃烧监控系统分析
加热炉燃烧系统工艺目的是使物料具有所要求的金属特性和热特性,且能量消耗、氧化和脱碳都控制在最小。系统针对坯料的钢种、进炉温度、产品尺寸及生产节奏确定最佳加热温度曲线,且在加热的动态过程中根据实际情况周期性修正设定值,以使实际的加热温度曲线和设定最大程度的吻合。
最佳加热温度曲线实际上是由静态的温度加热曲线和在实际控制中动态的修正以完成最佳加热温度控制的过程。在确定最佳加热温度曲线时,其控制要求呈多样性,诸如最大的产量、最小的燃料消耗、耐火材料和换热器的寿命、合适的出炉温度以及最小的脱碳和氧化铁皮损耗等等。显然,各种要求是有着互相制约的关系的,系统只能根据某种原则来进行最佳控制。加热炉燃烧系统采用了在确定的出炉温度前提下,对各控制段温度设定将使燃料消耗最少的原则。根据长期的经验以及实验用加热炉所获得的各种参数及数据,对应于不同的钢种、入炉温度、坯料形状和尺寸范围,并考虑到不同的生产节奏,计算出相应的最佳加热温度曲线,建立以上述各类变量为函数关系的数据库。
3 加热炉控制理论设计
3.1 基于bp神经网络的数学模型
(1) 确定输入层神经元数目。神经网络模型的输入层是起缓冲存储器的作用,把数据源加到网络模型上其节点数目取决于数据源的维数,即这些节点能够代表每个数据源。在轧钢加热炉生产的过程中,影响加热炉况的因素有很多,如:原燃料的物理性能和化学成分、气候条件、设备状况、加热炉运行状况等,这些因素的变化必然导致炉况的波动。因此,在诸多的加热炉操作参数中,选取9个与燃气量有密切相关的参数作为输入变量,分别为:空气量、炉膛温度、坯料在炉内位置及时间、坯料形状、炉墙和炉顶结构、耐火材料特性、烧嘴特性、燃料特性、坯料钢种。因此,输入层神经元数目为9。
(2) 确定隐含层神经元数目。网络的隐含层定为一层。隐含层神经元个数表达了网络输入与输出之间的非线性程度,对神经网络模型的训练速度和预报能力有着重要的影响,隐含层神经元个数少,不能满足精度要求,隐含层神经元个数多则影响训练速度。但是隐含层神经元的个数的选择没有一个统一的方法,只能依靠经验公式
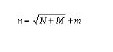
(式1)计算得到。本模型文中隐含层神经元个数n取11。
(1)
式中: n-隐含层神经元个数;
n-输入层个数;
m-输出层个数;
m-取1~8之间的整数。
(3) 确定输出层神经元数目
输出层神经元数目取决于神经网络模型的输出变量。本模型的输出变量为高炉故障,分别为:坯料内部温度、燃料的化学当量和废气平衡、氧化和脱碳、加热炉和坯料的热交换等。因此,输出层神经元数目为5。
3.3 bp神经网络模型的学习机理
对加热炉炉况进行分析的神经网络模型在前面已经阐述,我对武钢一号轧钢加热炉进行具体操作,得出数据。为节省篇幅,表中只列出5个输出样本,每个样本均有9个特征值,因而神经网络有9个输入节点。5个输出样本每个样本代表一种,因而有5种炉况。如果神经网络的每个输出节点代表一种炉况,则神经网络有5个输出节点。当神经网络的隐含层节点数为11、选择足够多的代表各种状态的样本、采用bp算法训练网络时,5个样本输出的对应网络输出如表1 所示。
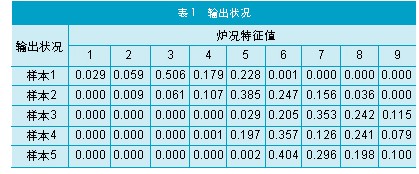
神经网络数学模型推理过程举例如下:根据本文炉况特点,当输出节点输出y接近1的计为1,其他计为0。当y=1时,说明加热炉况此时处于调节影响因素1(即把输出1反馈回去和输入相加后一起输入到控制器调节);当y=0时,说明不需要调节影响因素1(即不要把输出1反馈回去和输入相加后一起输入到控制器调节)。
3.4 神经网络训练
表2列出了试验过程中在上文中介绍的影响加热炉炉况的9种特征值经过归一化处理后的当量值,作为每个输出特征值。在本试验中,取网络的总误差允许值ε=0.00001。当对象发生具体偏差时,根据网络输出层节点的实际输出的数值来做出判断。例如,当第1个输出样本的9个输出特征值输入给网络输入层节点后,则得到网络输出层节点与其对应的实际输出为表中的第1影响因素的9个输出值,其中只有y1=0.9699,接近1,而其它输出均远小于0.9699,可以近似为0,所以用bp神经网络对加热炉的结论为“调节影响因素1” (即把输出1反馈回去和输入相加后一起输入到控制器调节)。
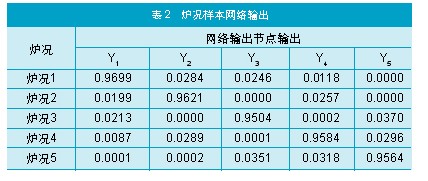
4 热炉炉温控系统设计
轧钢加热炉可分预热、加热、均热3个区域,8个燃烧控制段,采用平面烧嘴和火焰长度可调的直焰烧嘴。具体为预热段(顶部)4只,预热段(底部)4只;加热段(顶部)24只,加热段(底部)6只;均热段(左/右顶部)二段24只,均热段(左/右底部)二段6只。其每段控制回路均由软件实现,即采用西门子语言编程在s7-300可编程控制器(c-plc)协调完成各个燃烧控制回路的控制功能。
4.1 温度控制回路
各段的温度控制回路控制框图如图2所示。温度控制回路的温度设定可有二种方式,其一为远程设置,其二为本地设置。远程设置值来自监控计算机系统。本地设置值来自c-plc相应的mmi跟踪站,由操作工根据需要和经验设定。但监控计算机仍然进行实际钢温和最佳加热曲线所设计的钢温温差计算,但仅作为显示,不参与控制。
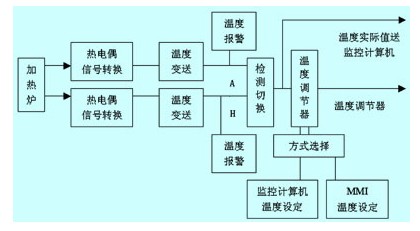
图2 温度控制结构框图
炉膛温度反馈通过双支热电偶采集后通过温度变送器直接输入c-plc。其后的各种处理则均以软件完成。温度报警中可设定温度的上下限值,当此值达到并持续确定的时间,系统将使相应的煤气切断阀动作,停止供热。热电偶两路采集为可靠起见,操作工可通过检测切换来选择通路a或通路b或二者取高值者作为温度实际值。
系统根据远程给定或本地给定和基于采集的温度实际值进行相应的数学计算产生的钢坯实际温度的偏差而给出控制调节器的调节输出量。
4.2 煤气/空气交叉限幅控制
在通常的燃烧控制系统中,采用串级比值调节系统。温度调节器的输出直接作为空气流量调节控制器的给定,然后空气流量实际值除以空/燃比作为煤气流量调节控制器的给定。在稳态时,煤气量可按一定的空燃比跟随空气实际流量而动,但在动态时,如升温、降温等变化时,这种常规系统就无法保证煤气量仍按一定的空燃比随空气量变化而变化。在轧钢加热炉燃烧控制系统中,采用了软件实现交叉限幅控制方式来保证无论在动态还是稳态时,都能满足一定的空燃配比性能。交叉限幅控制的基本原则是:升温时,空气先行;降温时,煤气先行。采用这种方式,使系统无论在稳态还是在动态时,都可获得较好的空燃比性能。同时由于没有过氧燃烧和缺氧燃烧而起到节能降耗的效果。从图3可见,系统通过高低选择器及其相应的空气和煤气实际反馈来完成升温空气调节先行,降温煤气调节先行的交叉限幅功能,达到控制目的。
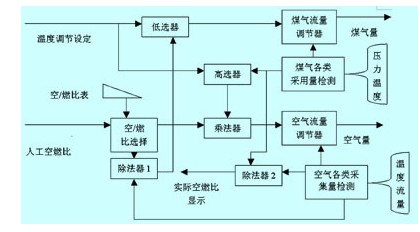
图3 煤气/空气交叉限幅控制回路结构框图
(1) 系统辨识(燃烧炉燃气/空气比值控制):
燃料流量被控对象为:
g(s)=(2/13s+1)*e-3s (2)
燃料流量检测变换系统数学模型为:
g(s) =1 (3)
燃料流量控制流量比值为:
g(s) =1/2 (4)
空气流量被控对象为:
g(s)=(3/11s+1)*e-2s (5)
(2)系统稳定性分析:
系统被控对象的bode图如图4所示,无调节器时,燃料控制系统开环稳定,幅值稳定裕量为11.4db,相位稳定裕量为97.1°,对应增益为3.72。
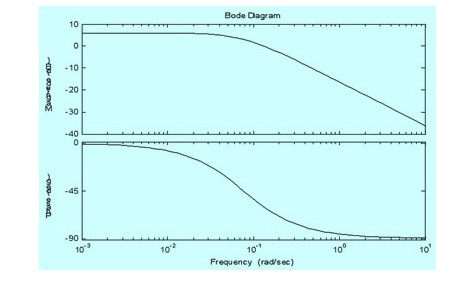
图4 燃气被控对象bode图
由图5可知,无调节器时,空气流量控制系统开环稳定,幅值稳定裕量为9.81db,相位稳定裕量为80°,对应增益为3.09。
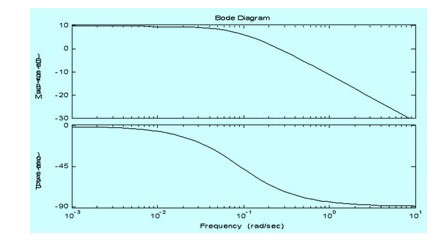
图5 空气流量被控对象bode图
4.3 控制系统参数整定
(1)燃料控制系统
为使系统无静差,燃气流量调节器采用pi形式,即:
g(s)=kp+ki/s (6)
其中,参数kp和ki采用稳定边界法整定。先让ki=0,调整kp使系统等幅振荡(由系统被控对象bode图知,在kp=3.72附近时系统振荡),即系统临界稳定状态。系统临界振荡仿真框图及其振荡响应如图6所示。
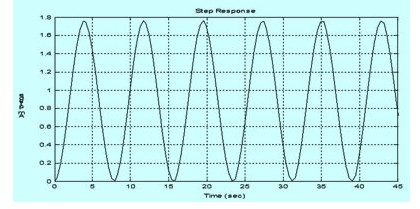
图6 系统临界振荡响应
记录此时的振荡周tcr=11s和比例系数kcr≈3.8,则kp=kcr/2.2=1.73,
ki=kp/(0.85tcr)=0.18。在kp=1.73,ki=0.18的基础上,对pi参数进一步整定,调节kp=1.1,ki=0.1系统响应如图7所示,可见系统有约10﹪的超调量。
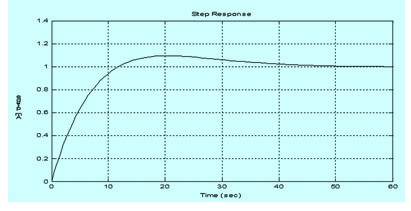
图7 燃烧控制流量闭环控制系统单位阶跃输入的仿真响应
(2) 空气流量控制系统
空气流量控制系统的整定方法和燃气流量控制参数整定方法类似,当ki=0.05和kp=0.08时,系统阶跃响应如图8所示,可见系统响应超调量约为25%。
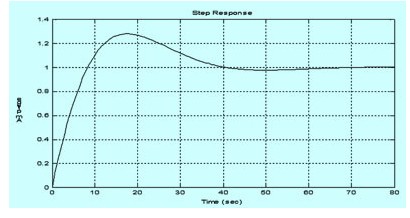
图8 整定后空气流量控制系统阶跃响应
4.4 炉温控制系统simulink仿真
图9为利用监控软件得到的炉温监控曲线。在设定温度为45℃时,利用智能pid调节器可以改变电磁阀的开度,以及调节热水与冷水间的交换速度,从而可以使温度基本保持恒定,此时的参数为(p=300
i=50 d="0"
sp=45),由于此时设定的温度较高,过渡时间较长,利用这种方法可以控制实际的加热炉的温度,使加热炉的温度保持基本稳定,对于实际生产有着重要的意义。
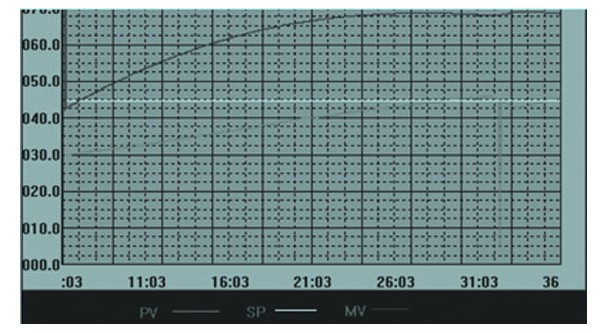
图9 炉温设定为45℃时的监控曲线
5 结束语
项目在系统的具体开发、设计和实现方面,运用模糊控制技术的理论,结合对当前加热炉的各种控制方法的控制性能、优点和缺点的分析,模糊控制器的设计及对模糊控制器的仿真实验结果,实验室实验及实际工程运用等情况作了说明。对于加热炉这种受随机因素干扰的、具有纯滞后的非线性分布参量的复杂的控制对象提出了一种新型的复合式智能控制算法—模糊pid参数自调整算法。对本文所提出的控制算法进行的大量的仿真试验,结果表明本文所设计的控制算法在自适应性、控制品质等方面较其它单纯算法有较显著的优点。