用“IPC”+“组态王”实现油墨生产线监控系统
发布时间:2006-07-20 来源:中国工控网
[编者按]:为推动组态软件在自动化行业的深入应用,自动化网特举办 “2005 自动化网杯 组态软件应用大奖赛”。欢迎大家参与投稿,稿件请发到:soft@zidonghua.com.cn ,并注明“自动化网杯组态软件应用大奖赛”![查看征文活动内容]
作者:张启军
摘要: 本设计主要针对我国当前中小油墨生产企业自动化程度不高,导致油墨产品质量不高的情况,以工控机(IPC)+ 组态软件 + 数据采集板卡实现油墨生产线监控系统。实现对生产线的实时监测管理、报警设置、趋势曲线、数据报表管理及打印功能。有利于实现企业管控一体化和ERP计划。
关键词: 油墨生产,IPC,组态王6.5,自动配料,数据采集
Abstract: This design mainly produces the medium small ink enterprise automation degree to current of our country not high, cause not high circumstance of the ink product quantity, Adopt the Industrial Personal Computer (IPC) + configuration software + the data collects the plank card to carry out the printing ink production line supervision system.Realization to production line of solid hour monitor management, alarm, trend curve, the data repot forms management and print the function.Be advantageous to carrying out the business enterprise control integral whole to turn and the ERP plan.
Key words: ink production, IPC , Kingview 6.5, Auto-blending,Data Acquisition
0.前言
为适应油墨工业发展的需求,我国的油墨生产和装备水平有了显著提高,但与国际先进水平相比仍有较大的差距。产品质量的优劣,很大程度上依赖于生产工艺、设备性能及自动化程度的高低。现代化的企业设备先进,自动化程度高,人的素质也相应的提高。有些油墨生产商目前存在的主要问题是生产设备老化、能耗高、效率低、自动化程度差、人工操作多等因素。其中生产自动化程度差,已直接或间接地制约了企业产品质量、操作人员的人身安全和身心健康。我们应意识到先进的设备监测手段、一流的产品检测、质量分析方法,都是企业产品质量、性能的保证,都将关系到企业的发展和生存。因此,在本次设计中,除了先进的生产工艺、生产设备外,选用先进的生产检测、产品计量、分析方法,大力提升企业生产的自动化水平,从而使企业彻底摆脱传统的、旧有的生产经营模式,为企业走向现代化的发展道路,迈出坚实的一步。
1. 工艺流程
油墨的生产大致可分为准备、配料、搅拌、轧研、校验调整、检验及装罐等工序。在油墨生产中,物料流程一般为:通过开袋机将进厂的所有粉状原料装入粉料仓,粉料仓再传输至日用量筒仓,以满足每天生产油墨所需的粉料。日用量筒仓有上下限控制,当粉料料位下降达到下限值时,系统会及时给以补充,当料位达到上限时停止补充粉料。油料也是如此。系统设计在每个料仓或罐体上装有称重传感器,根据上位机下传的配方自动启动进行配料的。粉料配好料后,由输送装置输送至混合罐,油料配好料后也送至混合罐。油料和粉料通过高速搅拌机在混合罐预混合后传至缓冲罐。缓冲罐的料是为研磨机所备,预混合料经过初、细研磨机研磨后,输送至调整罐,调整罐的墨即为基墨,基墨经检测后,人工计算出所需调整的油量,所需加的调整油通过下二次调整配方配料后,传至调整罐,待调整合格后即可出料。其工艺流程框图如图1.1 所示。
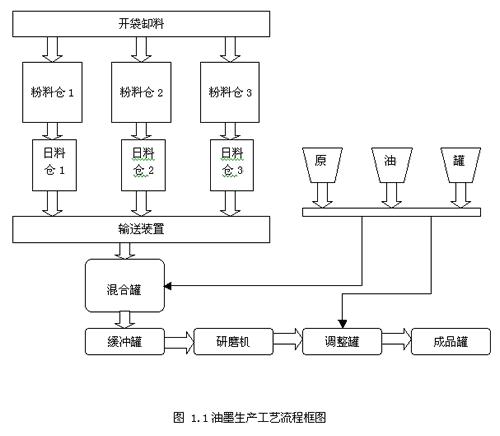
根据工艺控制要求提出测控点,绘制出带控点的工艺流程图如图1.2
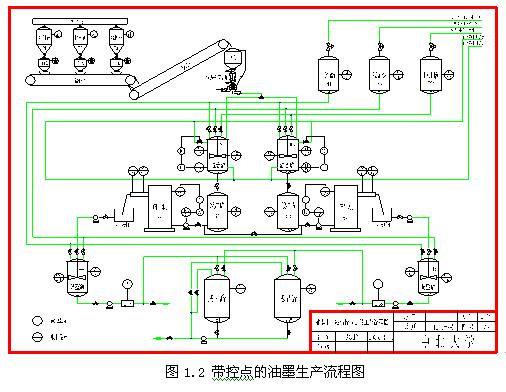
确定点数:
AI : 28路( 17路称重信号+ 4路温度信号+4路压力信号+ 3路粉料流量信号)
AO : 00路
DI : 36路( 22路输入输出调节阀开关量+10路设备状态量+4路继电器信号)
DO : 36路(同上)
2.系统组成
该系统采用集中控制,控制核心为工控机(IPC),通过传感器和变速器完成现场数据的采集,经数据采集板卡处理后送至工控机。通过工控机对采集数据的分析完成自动配料过程。并用组态软件“组态王”开发上位机监控系统管理软件。实现对生产线的实时监测管理、报警、趋势曲线、数据报表管理及打印功能。系统原理图见图2.1。
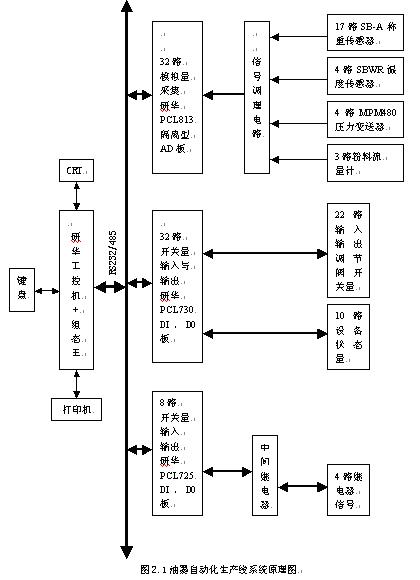
2.1系统配置
(1)现场工作站选用研华610工控机,研华工控机是我国台湾省研华工控公司的产品,其产销量都处于世界前列,产品性能稳定、可靠,具有良好的声誉。选用的工控机的配置如下:
Ø Pentium Ⅳ 2.0 GHz 字长32位
Ø 内存256M
Ø 硬盘 40G
Ø 17英寸三星纯平显示器 显存32M
Ø RS232串行口、打印机并行口、USB口、ISA、PCI插槽
Ø windows2000/xp操作系统 组态王6.5版运行软件
(2)UPS电源型号:C1K 额定容量:1kVA/0.7kW输入电压:(115~300)VAC 频率 (40~60)Hz(软件可调)
(3)打印配置
考虑到现场矿井提升设备只是打印日常的采集的数据、诊断结果的报表等,无需宽幅打印,配置性价比较高,而且在日常的打印中经常采用EPSON的。
(4) “组态王”硬件加密狗组态王软件通过硬件加密来防止盗版的,选用256点开发版、256点运行版。
(5)该系统模拟量采集选用研华PCL813隔离型AD板;开关量采集同样选用研华PCL730,32路DI、DO板;另加一块PCL725型DI、DO板,8通道。
(6)其它器件:SB-A 型称重传感器, SBWR/Z热电偶(热电阻)一体化温度变送器,MPM480压阻式压力变送器, 妙声力E系列粉料流量计。JZ7型中间继电器,DDZ-Ⅲ型调节控制器,气动电磁阀。
有条件的用户可配用PLC来实现数据的采集和部分控制任务,分散系统的风险,提高系统的稳定性。
2.2 通讯选择
选用RS485标准总线通讯,但因上位机的接口为RS232,所以还需一块RS232/RS485 双路转换卡来完成标准转换。可选用研华亚当4250构建电路实现RS232与RS485的标准转换。这里选用RS485的另一个原因是有利于以后网络系统的构成扩展。
3.系统软件设计
3.1油墨生产流程控制程序设计
程序分成8部分,即日用粉料仓补料程序,愿油料罐自补料程序,配方管理程序,混合罐自动配料程序(MT),混合罐搅拌程序,CO研墨程序,二次加料控制程序(LT),调整罐搅拌程序。现将每个程序的功能介绍如下
1. 日用粉料仓、原油料罐补料程序
所有的粉料仓都装有称重传感器,称重显示仪表安装于现场,以便于现场卸料人员观看,每个日料仓都设有上、下限控制,程序通过检测,会自动给日料仓补充粉料。原油罐与粉料仓相似,其自补料程序与粉料基本相同。
2. 配方管理程序
该程序的功能主要是通过组态王自带配方管理功能,通过函数调用配方、选择配方保存、删除配方,还可以添加配方来实现配方管理。详见配方管理功能。
3. 混合罐自动配料程序(MT)
该程序是整个工艺流程中最重要的部分,它的功能是完成对配料过程的控制。混合罐是高速预分散罐,混合罐上的搅拌器通过高速预分散将所配油料及粉料进行充分混合后,研磨机才可进行研磨,由于高速预分散是一个散热过程,所以混合罐上装有温度传感器,当温度高于混合罐的设定上限值时,系统打开冷却水阀门进行冷却,当温度低于下限时,关闭冷却水阀门。混合罐上装有上限保护开关及称重传感器,秤的实际值以千克值在上位机上显示,当液位低于某一参数值时,混合罐上的搅拌器关闭。通过混合罐底部称重传感器对所加料的检测,控制上端阀体打开或关闭,来完成配料的过程。具体分为油料配制,与粉料配置。两种配料过程是不同的,油料是分批次下料,料1下放完毕后关闭相应阀体,并启动料2的配制,料2完毕后启动料3,料3完毕后,关闭相应阀体,油料配制完毕,启动粉料的配制。粉料的下料是通过粉料流量计的,因此可以三种料一起下放,谁先到达预定值,就相应停止该料的下放。程序流程见图 3.2。
4. 混合罐、调整罐的搅拌程序
搅拌程序是对电机的控制,和搅拌时间的控制。只有达到相应的条件才能进行搅拌,时间的控制,这里是一个延时程序控制,程序比较简单,这里不再赘述。
5. CO研墨程序
该程序是通过检测判别相应的进出口压力、温度及上面缓冲罐的料位情况来决定研墨机和进料泵的启停。
6. 二次加料程序程序
当一个批次研磨完后,由检测人员进行检测,通过计算,如果需要调整,则必须创建一个调整工序,调整工作配方输入后,控制系统自动启动二次加配料程序并将所配料排至目标罐。二次加料的控制程序与混合罐配料程序有相似之处,并且比混合罐配料程序更简单,因为没有粉料的配制。这里不再赘述。
程序流程图如下:图3.1油墨生产控制主程序流程图
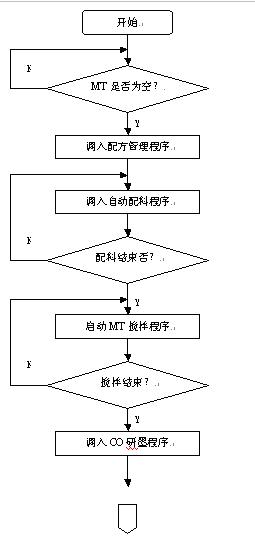
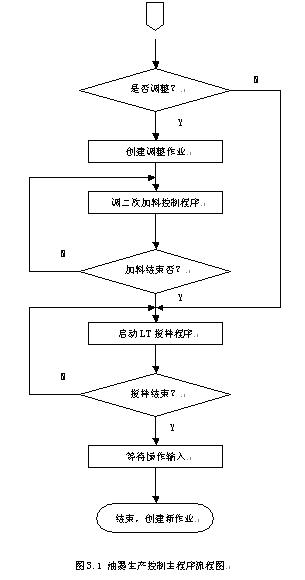
下面是配料控制程序流程图:
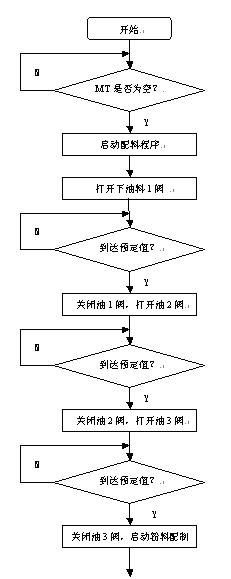
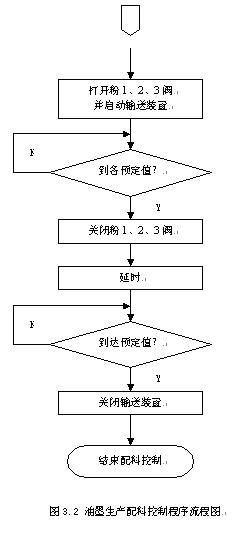
3.2 应用组态王开发监控系统软件
新型的工业自动控制系统正以标准的工业计算机软、硬件平台构成的集成系统取代传统的封闭式系统,它具有适应性强、开放性好、易于扩展、经济、开发周期短等优点。通常可以把这样的系统划分为控制层、监控层、管理层三个层次结构。其中监控层对下连接控制层,对上连接管理层,它不但实现对现场的实时监测与控制,且在自动控制系统中完成上传下达、组态开发的重要作用。
选用北京亚控组态王6.5版软件256点开发版、256点运行版。
建立应用工程的一般步骤:
a.设计图形界面 b.定义设备 c.构造数据库变量 d.建立动画连接 e.运行和调试
这五个步骤并不是完全独立的,事实上,这五个部分常常是交错进行的。在用TOUCHMAK构造应用工程之前,需要仔细规划项目,主要考虑三方面问 :画面;数据;动画。通过对监控系统要求及实现功能的分析,采用组态王对油墨生产线监控系统进行设计,系统组态结构如图3.3
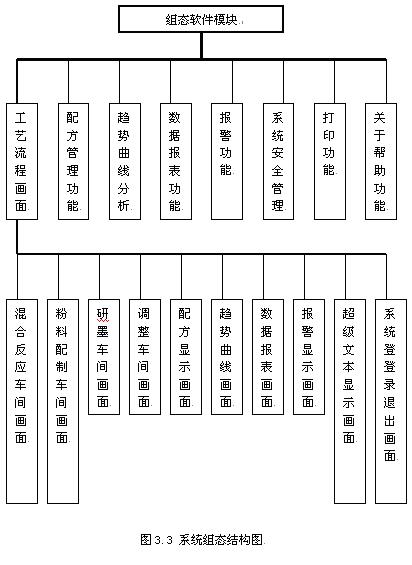
★★ 系统开发过程步骤
★ 定义设备
组态王把那些需要与之交换数据的设备或程序都作为外部设备。外部设备包括:下位机(PLC、仪表、模块、板卡、变频器等),它们一般通过串行口和上位机交换数据;其他Windows应用程序,它们之间一般通过DDE交换数据;外部设备还包括网络上的其他计算机。
只有在定义了外部设备之后,组态王才能通过I/O变量和它们交换数据。通过“设备配置向导”就可以简单的完成外部设备的连接。
※※在进行各个外部设备定义之前,需要确定该设备的驱动已经安装,如果使用Windows NT系统,还需要安装系统补丁。
1、模拟量数据采集卡PCL813的定义
①在组态王工程浏览器的左侧选中“板卡”,在右侧双击“新建”,运行“设备配置向导”;
②选择“研华”,“PCL813”,“板卡”,单击下一步,打开逻辑名称设置对话框;
③外部设备取名“PCL813”,单击下一步,打开设备地址,初始化设置对话框;
④组态王定义PCL813设备的地址格式为 十六进制数, 设地址为304,无初始化字。单击下一步弹出信息总结对话框。确认无误后完成即可,否则可返回上一步,重新设置。
2.数字量采集输入输出板卡PCL730 、PCL725的定义
定义过程与PCL813基本相同,只是信息设置地址不同而已。这里就没必要在叙述了。
★ 构造数据库变量
数据库是“组态王”最核心的部分。在TOUCHVEW运行时,工业现场的生产状况要以动画的形式反映在屏幕上,操作者在计算机前发布的指令也要迅速送达生产现场,所有这一切都是以实时数据库为中介环节,所以说数据库是联系上位机和下位机的桥梁。
数据库中变量的集合形象地称为“数据词典”,数据词典记录了所有用户可使用的数据变量的详细信息。
在组态王软件中数据库分为:实时数据库和历史数据库
数据库中存放的是制作时定义的变量以及系统预定义的变量。变量可以分为基本类型和特殊类型两大类。基本类型的变量又分为“内存变量”和“I/O变量”两类。基本类型的变量也可以按照数据类型分为离散型、模拟型、长整数型和字符串型。
特殊变量类型有报警窗口变量、报警组变量、历史趋势曲线变量、时间变量四种。这几种特殊类型的变量正是体现了“组态王”系统面向工控软件、自动生成人机接口的特色。
在工程浏览器的左侧选择数据词典,在右侧双击新建,就可以打开数据属性设置对话框,进行变量的定义。
以每种类型一个变量为例,我们简单介绍下变量的具体设置:
1、内存离散变量、I/O离散变量
内存和I/O离散变量的区别是否与外部设备连接,其他设置基本相同。
以下油料阀11为例,定义变量的基本属性如图 3.4所示:
连接设备选择PCL730,寄存器格式:DIdd,dd表示数字量输入通道,取值范围0~31。如上图的下油料阀由第8路输入,因此写为DI08。依照寄存器类型选择数据类型Bit。
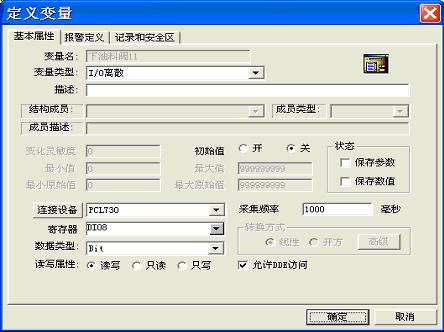
图3.4 定义IO离散变量
2、内存实型变量、I/O实型变量
内存和I/O实型变量的区别同样在于是否与外部设备连接,其他设置基本相同。以混合罐1的温度为例,定义IO变量的基本属性、报警定义、记录。
※ 需要注意的是,最小值、最大值、最小原始值、最大原始值的设置。
Ø 最小值:该变量值在数据库中的下限;
Ø 最大值:该变量在数据库中的上限;
Ø 最小原始值:与前面定义的最小值所对应的输入原始模拟值的下限
Ø 最大原始值:与前面定义的最大值所对应的输入原始模拟值的上限
如温度传感器的输入范围为0~5V,温度范围为0~100℃。因此最小值为0,最大值为100。PCL730为12位的数据采集卡,因此输出范围为0~4095,所以最小值为0,最大值应为4095。
连接设备选择PCL813,寄存器格式:ADdd,dd表示模拟量输入通道,取值范围0~31。如上图的下温度由第6路输入,因此写为AD06。依照寄存器类型选择数据类型SHORT。定义属性如图3.5
记录与安全区中,定义数据变化记录,即只要数据发生变化就进行记录。
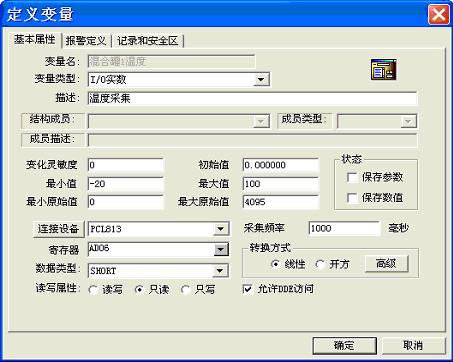
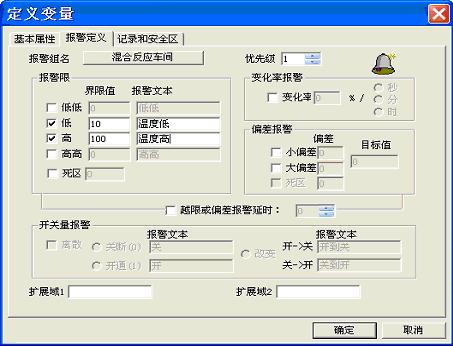
图3.6 定义变量报警设置
根据温度允许范围,在报警定义中,确定报警界限值低为10,报警文本为“温度低”;高为100,报警文本为“温度高”。
★ 画面生成动画连接
开发者在TOUCHMAK中制作的画面都是静态的,需要通过实时数据库,因为只有数据库中建立的变量才是与现场状况同步变化的。数据库变量的变化又通过“动画连接” 导致画面的动画效果。所谓“动画连接”就是建立画面的图素与数据库变量的对应关系。这样,工业现场的数据,比如温度等,当它们发生变化时,通过设备驱动,将引起实时数据库中相关联变量的变化。 动画连接的引入是设计人机界面的一次突破,它把程序员从繁重的图形编程中解放出来,为程序员提供了标准的工业控制图形界面,并且通过内置的命令语言连接来增强图形动画效果。
下面介绍几个主要画面的开发与动画连接过程:
混合反应车间画面:该车间是油墨生产线的主要反应部分,涉及的监控量较多,是生产的主要环节,如图 3.7。 搅拌器旋转的动画实现:
首先利用画多边形工具画出叶轮样子,复制成六个,改变不同的视角形状,生成六个不同形状的叶轮,编号为0到5。定义整型内存变量“动作状态” ,在应用程序命令中编制下列循环程序:
if(\\本站点\动作状态<5)
{\\本站点\动作状态=\\本站点\动作状态+1;}
else{\\本站点\动作状态=0;}
该程序是实现变量“动作状态”的从0到5的自增1循环程序。
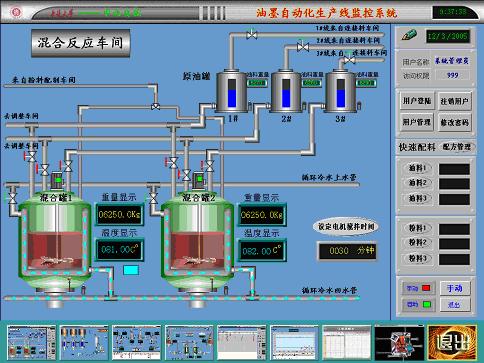
图3.7 混合反应车间监控画面
针对每个叶轮设置隐含属性条件如图3.8。对于0号叶轮设置成:
\\本站点\动作状态==0||!\\本站点\搅拌电机1
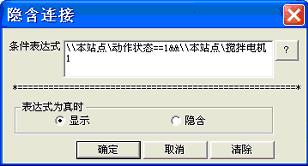
图3.8 叶轮隐含属性设置
然后将这六个叶轮相互重叠放置在一起,保存画面,运行后即可见到。水流的动画实现与叶轮的原理相同。
混合罐料位的缩放动画:
由于罐体是自己画的,没有填充功能。现利用缩放功能实现料位的动画效果。双击该点位图,弹出动画连接对话框,点击缩放按钮,弹出缩放连接对话框如图 3.9。设置表达式如图,填写对应的数值即可。
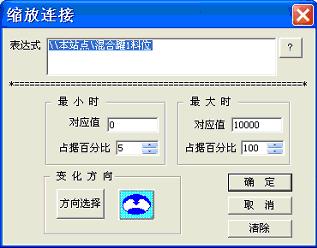
图3.9缩放连接
模拟值的输入输出显示:
在画面上输入字符###(其它也可),双击进入动画连接对话框,点击模拟值输出,弹出如图 3.10的对话框,设置如图。当然改变量必须设置成可读可写型。模拟值的输出显示与输入类似,只是如果不需要同时输入模拟值时,设置成只读型即可。并设置输出数据位数,显示方式。至于其它离散量的连接比较简单。
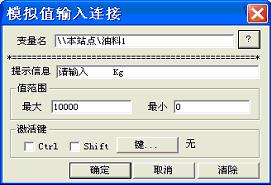
图 3.10 模拟值输入连接
★ 系统管理功能配置
1. 配方管理
实现对油墨生产的配方管理工作,可以显示存入系统的全部油墨配方,调用系统定义的配方,也可以根据生产过程的要求自己增加新配方。方便了配方的管理和应用,使配方的调用和修改更加灵活。配方管理画面如图 3.11
针对本系统的实际情况,定义了配方文件“油墨配方.csv”并与相应的配方函数实现对配方的管理和操作。定义了调入配方、选择配方、保存配方、删除配方、确定、以及添加配方功能。
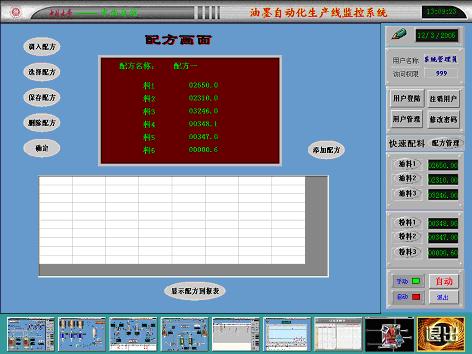
图3.11 配方画面
2.报警功能
报警是指当系统中某些量的值超过了所规定的界限时,系统自动产生相应警告信息,表明该量的值已经超限,提醒操作人员。报警的显示比较简单,采用组态王中的报警控件即可。声音报警需进行编程设置。例如:温度高声音报警
{ string soundname;
soundname=InfoAppDir()+"wendugao.wav";
PlaySound( SoundName, 1 );}

图3.11 研墨车间监控及其报警画面
并对其属性进行些设置如图3.12 。
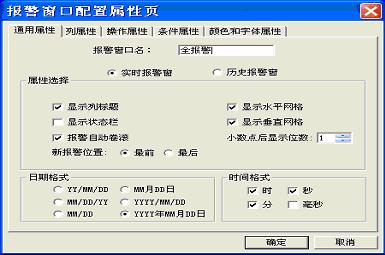
图3.12 报警设置属性
本设计根据每个车间设置了报警组,并针对研墨车间单独创建了报警画面,这里需要说明的是在设置需要报警的变量时必须对其进行报警设置和记录设置(可参考前面的变量定义图 3.6),才能把该变量的报警显示到画面中。
3. 报表功能
数据报表是反应生产过程中的数据、状态等,并对数据进行记录的一种重要形式。是生产过程必不可少的部分。它既能反映系统实时的生产情况,也能对长期的生产过程进行打印、统计、分析,使管理人员能够实时掌握和分析生产情况。
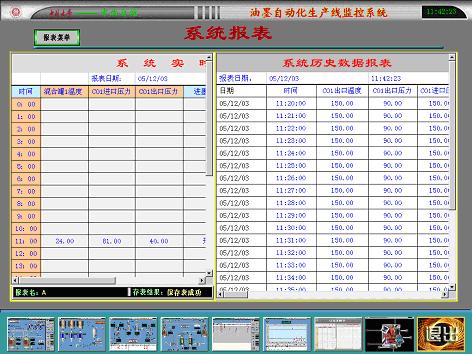
图3.13 系统报表画面
4. 趋势曲线分析功能
该画面是对现场数据的采集形成曲线表达,更形象直观的看出数据的发展趋势,分历史曲线与实时曲线,即能得到实时值,还能对历史数据进行查询打印功能。通过曲线切换按钮,曲线可以在历史曲线和实时曲线中切换,如图3.14、3.15所示。曲线切换菜单的命令语言如下:
if (menuindex==0)
{ k1=1;}/*实时曲线*/
if (menuindex==1)
{ k1=0;}/*历史曲线*/
在画面命令语言中设置:if(k1==1)
{Ctrl4.HTUpdateToCurrentTime();}/*使控件的右指示器永远指向当前值*/
这样,在对菜单进行切换时,就能实现两种曲线的切换。
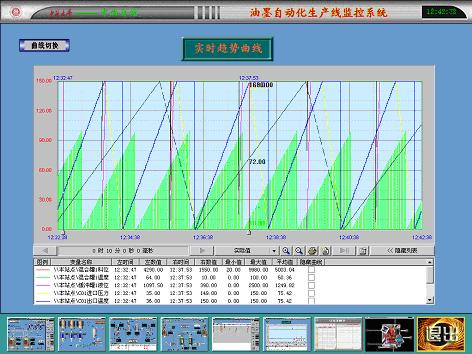
图3.14实时趋势曲线画面
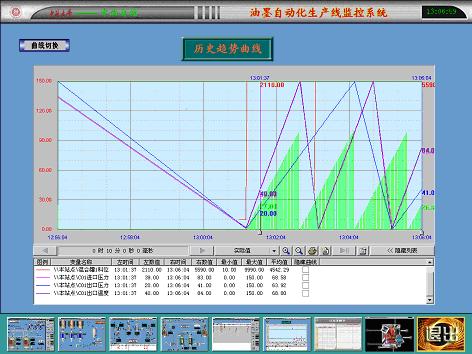
图3.15 历史趋势曲线画面
5.安全管理功能
安全保护是应用系统不可忽视的问题,对于可能有不同类型的用户共同使用的大型复杂应用,必须解决好授权与安全性的问题,系统必须能够依据用户的使用权限允许或禁止其对系统进行操作。在“组态王”系统中,在开发系统里可以对工程进行加密。打开工程时只有输入密码正确时才能进入该工程的开发系统。对画面上的图形对象设置访问权限,同时给操作者分配访问优先级和安全区,运行时当操作者的优先级小于对象的访问优先级或不在对象的访问安全区内时,该对象为不可访问,即要访问一个有权限设置的对象,要求先具有访问优先级,而且操作者的操作安全区须在对象的安全区内时,方能访问。
系统登录:在Touchvew运行环境下,操作人员必须以自己的身份登录才能获得一定的操作权。
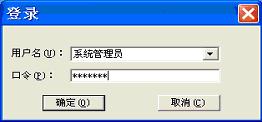
图 3.16 登录对话窗
单击用户名下拉列表框显示在开发系统中定义的所有用户的用户名称,从中选择一个;在“口令”文本框中正确输入口令,然后单击“确定”按钮。如果登录无误,使用者将获得一定的操作权。否则系统显示“登录失败”的信息。
密码修改:在运行环境下,“组态王”还允许任何登录成功的用户(访问权限无限制)修改自己的口令。首先进行用户登录,然后执行“修改密码”菜单,则弹出如图 3.17所示。
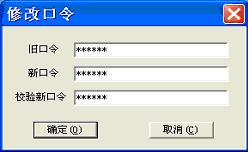
图3.17 修改口令对话窗
在“旧口令”输入栏中输入旧的口令, 在“新口令”输入栏中输入新的口令,在“校验新口令”输入栏中同样输入新的口令,给用户一次核实的机会。最后单击“确定”按钮,然后旧的口令将被新的口令所代替。
管理定义用户:
运行系统中,对于操作权限大于900的用户还可以对用户权限进行修改,可以添加、删除或修改各个用户的优先级和安全区。如图 3.18。
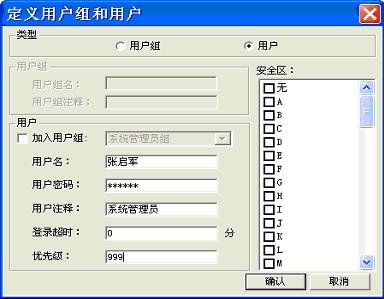
图 3.18管理定义用户对话窗
★ 仿真演示与实际运行调试
仿真演示
软件程序设计完毕后必须进行运行调试才能验证开发制作的如何,并检查错误漏洞进行修补。此过程是一个反复试验反复修改的过程,比较繁琐。由于仿真技术的发展,现在许多程序可以先进行仿真试验后再进行实际运行调试,这样给程序软件的开发带来了很大方便,缩短了开发周期,减少了开发费用。组态王提供一个仿真PLC设备,用来模拟实际设备向程序提供数据,供用户调试。它虽不能代表实际运行的结果,但能从某种程度上反应运行结果情况。
只是从某种意义上可以代表运行情况,不会和实际完全吻合。仿真缩短了开发周期,避免现场调试去修改那些不必要的错误而花费大量时间,但它并不完全代表实际,一切实际工程调试应以现场调试为准。
对仿真的说明:
采用仿真PLC主要来完成对画面动画效果的检验,对于生产控制流程的控制效果不会像实际运行调试的结果那样,这是因为组态软件的目的并不是为了仿真,也就是说它不是仿真软件,它只不过有部分仿真的功能。一切运行效果应该以实际运行调试为准。切不可为了追求某种动画效果而大用内存点数,或进行某些不合实际的盲目修改参数。这样一是带来点数的增加(组态王是按点数出售的)珍惜每一个点数,二是这不符合工程实际要求。仿真只能代表一部分,不是全部真实情况。一切应以实际实践为准,记住实践是检验真理的唯一标准,记住这句最熟悉,最见效的话。
实际运行调试
经过反复修复和调试,达到了预期的目的和功能效果。通过观查各画面显示效果可以看出个动画连接无误,能正常反映基本运行情况。搅拌电机、冷水阀、下料阀、补料阀开关等能按要求进行动作。能各输入输出量都可显示,报警的各变量都按预定值进行报警显示。配方管理、报表系统、趋势曲线能正常运行显示,可以进行查询、打印实时观看曲线走势。各功能按钮均可正确执行,系统安全功能正常工作。运行一年来没有大问题出现,运行状况良好。
4.结束语
虽然如今工业控制自动化技术发展的形式多样,但对我国走低成本自动化中小油墨生产企业来说,寻找一个合适的自控系统还是不容易的。本系统的设计兼顾了技术与经济,具有很好的性价比。以工控机(IPC)+ 组态软件 + 数据采集板卡实现油墨生产线监控系统。看似是一个集中控制系统,其实它的主要控制任务还是有本地电气控制柜来完成的,上位机的作用是偏向于监测的,希望通过对这些油墨生产企业的自动化技术改造,预计能达到以下效果:基本上杜绝由于人工配料时偶尔出现错误时所造成的浪费。配每一批料和每一种料的数据都记录在案,并有日期、批数及数据都可查,记录可保持时间自定。这些数据的保存能使我们及时的发现问题和得到纠正,使用自动称量配墨装置对油墨质量的一致性和稳定性有根本地保证,杜绝人为因素所带来的费。可以基本满足生产要求与市场需求。
本监控系统是由本人在中北大学时针对太原某油墨厂技术改进工程,利用“组态王”开发的专门应用于油墨自动化生产线,对生产线进行监测管理。本软件可对现场车间的生产情况进行实时监测,并具有部分控制现场操作的功能。并且对现场的数据采集进行生成报表、曲线,便于操作人员进行数据分析,以便改进工艺参数。这些参数是很有用的,它是产品质量提高的关键。从某种意义上,本软件充当了从工厂到市场的中介,为实现企业的ERP做了很好的基础。由于本人水平有限和时间的限制本软件设计还有不少缺陷,像后台数据库的开发在,与DDE设备通讯,本软件中就没设计,希望在今后改进,开发出更好的系统管理软件。希望大家给予批评指正。
谢谢!!!
参考文献:
[1] 黄改娟.PLC可编程控制器在油墨自动化生产线的应用. 科技情报开发与经济.2003.06
[2] 付家才.工业控制工程实践技术.北京:化学工业出版社.2003.7
[3] 曲波,肖圣兵.工业常用传感器选型指南。北京:清华大学出版.2002
[4] 欧金成,欧世乐,林德杰. 组态软件的现状与发展. 自动化博览, 2002.1
[5] 组态王6.5使用手册. 北京亚控科技发展有限公司