封面故事:机器人的革新和安全性
发布时间:2013-09-18 作者:Mark T. Hoske
新的机器人安全性规范正在筹划中
机器人的安全规范越来越多,并引入了一些先进的机器人技术,包括合作机器人。
当所有企业都能够满足包括机器人安全标准在内的各种标准时,商业应用就能更加平稳。安全标准能够降低人员生命风险和问责风险,帮助满足市场需求,还能够通过标准化的设计和生产来降低成本。C&S Wholesale Grocers 公司的安全认证总监Roberta Nalson Shea,同时也是Symbotic LLC公司的安全认证总监,她说道,全球统一的标准能够降低设备集成商和最终用户的成本。
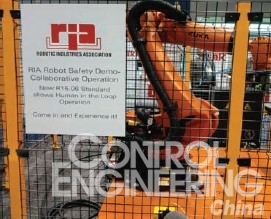
机器人工业协会在2013年自动化展上演示了新的R15.06标准如何在循环作业中确保人员安全;防护网后面是一台Kuka机器人。
同时,作为RIA机器人安全标准委员会的主席,Nalson Shea说最近机器人工业协会(RIA)机器人安全标准委员会向美国国家标准协会(ANSI)提交了对ANSI-RIA机器人安全标准(R15.06-2012)的更新。此更新标准直接采纳ISO 10218-1机器人和第二部分集成的内容,并增加了R15.06的介绍部分和文献部分。它能够帮助机器人生产厂商、其他设备建造商、系统集成商和最终用户,因为它使世界向着全球统一的机器人安全标准又迈进了一步,带来了成本的降低。它提高了安全功能,包括对于工作状态下人员不能靠近的机器人,以及那些将会与人员在同一个区域内工作的“协作”机器人。标准中提及的操作人员代表所有人员,并不仅仅代表机器人的操作员。R15.06-1999可以使用到2014年底。
其他ISO安全标准包括正在筹划中的关于合作机器人(Collaborative Robot)的技术规范(TS)15066,包括力和功率限制的规定。Rethink Robotics公司和Universal Robots公司的机器人能够在遭遇阻挡的时候停止动作,降低对工作于同一区域的人员所带来的风险。她说,ABB和Kuka公司也在开发这种产品。
使用机器人进行甜菜优化分析(Kristian Hulgard)
在没有机器人专家在场的情况下,Nordic Sugar公司就可以在经销商的帮助下安装用户友好且可靠性不错的合作机器人。
Nordic Sugar公司在研究新一代的机器人,希望能够实现原材料样本分析过程的自动化,最重要的前提是灵活性和友好的用户体验以及合理的价格区间。三台机器人协同作业,员工可以很容易地对分析过程进行调整,无需咨询机器人专家。位于瑞典Örtofta的Nordic Sugar AB工厂是欧洲最大的糖厂之一,每年从九月中旬到第二年的一月中旬,它都需要一周七天、一天二十四小时地运转,对来自于大约2000个瑞典甜菜种植户的每天600次的甜菜送货进行处理。
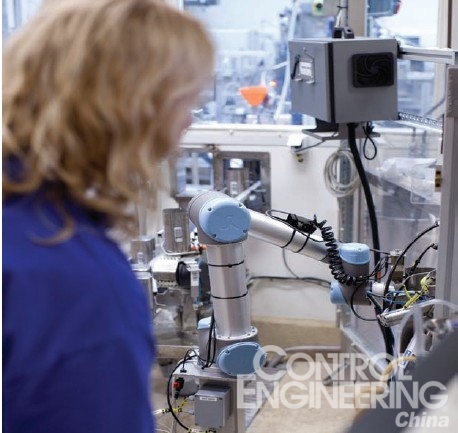
现在NordicSugar公司的雇员能够使用UR机器人直观的用户界面对机器人进行编程,无需向机器人专家寻求帮助。无需安全防护,雇员可以在生产过程中对机器人进行监控,测试糖罐容量以及糖向过滤器的流动情况。
“为了确保每一个种植户能够正确收到原材料的付款,我们会分析甜菜的含糖量和浓度,”Nordic Sugar AB工厂测试部门的生产和分析经理Bo Bergdahl说道。在长达四个月的收获季,我们对45000个样本进行分析,部门还会为合作伙伴进行35000次样本分析。
Bergdalh在1993年为单调的工作引入了机器人,采用了喷涂房的设计思路,不过哪怕一个很小的软件改动也必须引入咨询服务,为了实现安全防护采用了树脂玻璃和光束,机器人零部件的更换成本也很高。
在新糖度分析机器人上市之后,Nordic Sugar公司目前已有三台这种机器人在运行,预计在未来两年还会增加三台机器人,以替换上一代的机器人。机器人扫描条形码然后夹取装有糖的容器进行从称量到过滤的分析步骤然后送回原处。这个过程由气动夹爪和条形码扫描仪完成,还包括机器人手臂终端的工具。这些机器人的成本较低,AH Automation公司的Peter Johansson说道,AH Automation公司就是安装Nordic Sugar公司最新一代机器人的经销商。
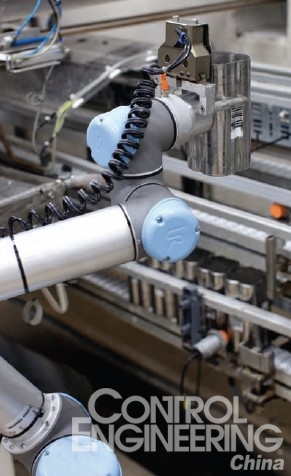
“今天,如果我们需要重新定位机器人或者更改机器人的速度,我们自己就可以完成,”Bergdahl说道。新型机器人代替了其他的机器人。“现在,我们可以将资金用于购买新的机器人而不是购买零配件,”Bergdahl说道。一旦发生了触碰事故,机器人输出的力低于EN ISO 13850标准中规定的150牛顿。最终受动器和其他环境条件也会带来危险,因此必须进行风险分析。(经过1600个应用项目的统计,Universal Robots公司80%的机器人并不需要防护网。)
机器人协同作业的六个要点
Rethink Robotics公司的董事长和首席技术官 Rodney Brooks解释道,机器人并不需要比自己更加聪明的使用者,它们只需要有与使用者的能力相匹配的用户界面即可。重新设计机器人的界面,使其更类似一个游戏控制器而不是一个麻省理工学院工程师的大脑,用户能够在5分钟内掌握机器人85%的功能。Brooks说道,合作机器人应该:
1)无需集成;完整的系统应该开箱即用;
2)无需编程或者培训,只需几分钟就可以使用;
3)功能多样;
4)智能作业,了解其作业环境,包括自动故障恢复;
5)即使操作人员遭受机器人的全速冲击也能确保安全。
6)具有可扩展的平台。
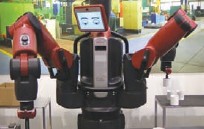
Rethink Robotics公司提供一种被称为Baxter的机器人,它是一种便于编程和使用的合作机器人,可以与人在同一区域安全地作业。图片来源:CFE Media
开源机器人软件的最新进展
ROS-Industrial联盟(RIC)是由14家旨在通过ROS-Industrial开源软件促进先进制造技术的组织构成。
ROS-Industrial联盟(RIC)于2013年3月6日在美国德克萨斯州San Antonio的西南研究院(SwRI)召开的年会上,介绍了开源机器人软件的最新进展,来自14家企业的25名代表出席了会议。RIC是一个自动化研发组织的国际联合网络,旨在通过ROS-Industrial开源软件促进先进的生产制造技术。
会议中详细介绍了SwRI、ROS、MoveIt!、ROS-Industrial和RIC。Willow Garage公司的Sachin Chitta博士解释道,与会人员大多数来自于工业界,他们表达了对于ROS-I潜力的热情以及对于被称为MoveIt!的未来ROS运动规划(motion planning)应用的关注。MoveIt!软件框架将会被用于ROS的运动规划(它是ROS平台的核心组件之一)。
Motoman Robotics美国公司(Yaskawa旗下公司)的技术总监Erik Nieves借助其远程监控机器人讨论了ROS-Industrial对于机器人原始设备制造商的价值。Nieves说道:“ROS-Industrial是一项重要的工作。确实,我们需要一个坚实稳定的ROS版本,所以Yaskawa让我们参加了ROS-Industrial联盟。”
在SwRI的生产制造系统工厂中,SwRI对5个支持ROS-I的机器人进行了演示。HDT机器人展示了其远程操控便携机器人手臂。

成员会议中,与会人员分享了在工业机器人研发中使用ROS/ROS-I的经验。ROS-Industrial的创始人Shaun Edwards为ROS-Industrial的未来发展绘制了蓝图。与会人员被分成小组,针对ROS-Industrial的规划给出反馈。
Fraunhofer IPA公司机器人和辅助系统部门负责软件工程和系统集成的集团经理Ulrich Rieser做了主题介绍,他作为“ROS-I欧洲代表”给出了ROS-I在欧洲的发展蓝图。
5个潜在项目
RIC项目经理Paul Hvass解释了聚焦技术项目(FTP)的工作状态,以及他们如何使成员企业分担开发新ROS-Industrial功能的成本。联盟成员展示了5个FTP项目:
1)用于ROS的图形编程用户界面;
2)基于Movelt!的移动操作演示案例;
3)基于Movelt!的修边演示案例;
4)用于修边/夹持作业的能够控制作用力的远程操控系统;
5)用于叉车升降机/AGV安全的人员跟踪系统的改进。
当大多数成员企业同意进行立项,那么这个FTP项目就可以开始。
汽车制造商通过电动夹爪降低成本(Bryan Morehouse)
作为汽车制造企业自动变速器操作策略的一部分,原始设备制造商通过使用电动夹爪从而省去了设备变更的高昂成本。
为了满足全球化生产对于灵活生产的需求,一家世界上最大的汽车制造企业最近与位于美国密歇根州Dexter的Moore Controls公司携手,提供新型的物料夹持系统,为自动变速器的生产服务,它能够从不同的生产车间运送工件,从钢板到成品齿轮,以便于后续组装。
“传统的齿轮夹持系统可以长期对一种零件进行夹持,”Moore Controls公司的总裁Steve Moore说道:“产品变更是非常耗时耗力的,且会对产量造成影响。当今的全球市场要求汽车生产企业具备一种系统,在无需做额外的配置和变更的情况下,就能够灵活的操控大量的零部件。”

自动化基座上安装有两个Festo伺服爪和安装于Festo气缸上的V型手爪,一个电动手爪爪用来夹持成品零部件,另一个电动夹爪用来完成原料替换。从自动化基座的伺服电动夹爪背面可以看到电动夹爪的电源和通讯电缆。图片来源:Festo
Moore选择二指平动手爪,使用24V直流电机,配有用于电气控制的编码器。电动夹爪安装于不同的基座、机器人和模块框架上,可以适用于每一个生产车间。每一个模块车间使用最少两个电动夹爪,有的车间使用多达5个电动夹爪;集成自动化站点的完整的物料夹持流水线使用上百个电动爪。
这些站点中最常见的应用就是“灵活自动化车间”,电动夹爪安装于标准气动组件上:用于实现零部件水平和垂直翻转的ISO气缸、阀岛和气动部件。两组电动夹爪安装于气缸上,两者之间成90度夹角,一个用来寻找齿轮的外沿直径,另一个用于进位,准备夹持下一个齿轮,实现稳定的生产作业。电动夹爪夹住每一个齿轮的外沿,所以它能够精确测量齿轮的直径,辨别出可能在人工加料过程中引入的尺寸不同的齿轮。
为了通过编码器反馈来测量并识别出每一个齿轮,电动夹爪通过伺服电机和PLC控制的滚珠丝杠来实现电气控制。每一个车间内,电机控制器都通过搭载了ProfiSafe设备安全协议的Profibus网络来进行通讯,PLC计算手爪的绝对位置并发送指令,以实现零部件夹持和测量作业。