超超临界汽轮机在不同运行条件下的高效设计方案
发布时间:2010-06-18 www.cechina.cn
未来,燃煤所产生的碳排放物可以进行收集和贮存,但如今更好的方式是采用高效燃烧技术来减少碳排放。其中,超超临界技术可以用较低的电力生产成本提升新建电厂的效率,同时从根本上减少燃煤发电产生的碳排放量。
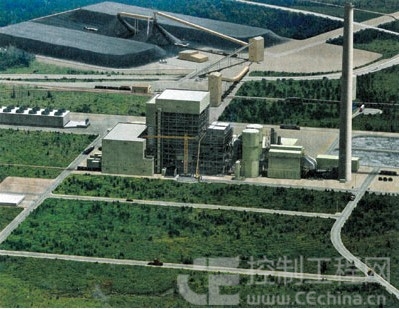
图1 将于2012年投入商业运行的AEP John W.Turk, Jr.电厂,将成为美国首个且惟一的超超临界电厂
对于每个有环境意识的公用事业公司来讲,他们的目标是通过推进技术进步和提升电厂效率来减少环境污染和降低燃料消耗。而实现这一目标的方法之一,是选用可在超超临界(USC)蒸汽工况下运行的燃煤蒸汽发电设备。在极高的压力和温度下,使用较高热值煤种的燃煤电厂可实现超过44%的净电厂热效率,而未来10年内的技术开发,也正积极瞄准达到或超过48%这一净电厂效率目标。

图2 TPP汽轮机采用一种冷凝式串联单再热设计方案。其中包括一台四缸体汽轮机,含有一台单流式高压汽轮机、一台双流式中压汽轮机和两台双流式下排气低压汽轮机。此汽轮机在3600rpm下工作
在本文中,我们将展示一座美国新建USC项目在提升汽轮机运行条件后的成效,以及通过此项先进设计所能减少CO2的排放量。
错综复杂的煤炭难题
煤炭在美国是一种十分具有吸引力的发电能源,主要因为其具有很好的实用性和预计250年的地下储存量。公用事业公司需要努力满足不断增长的电力需求,所以燃煤发电仍然具有相当的经济性,同时作为备受青睐的燃料来源,煤炭仍将占据美国发电能源份额的50%。

图3 TPP蒸汽循环在HARP配置下采用了8个给水加热器。经优化的蒸汽循环如图所示,同时附上平均工况下获取的数据作为加热率的保证值
然而,燃煤电厂目前正经历着十分严格的审查,并承受着进一步污染排放量受限和温室气体排放控制的强大政治压力。当前,全球30%的CO2排放量来自电厂,而美国绝大多数的电厂平均厂龄都超过了30年。据估计,如果将世界上全部现有电厂用最新且最高效的电厂取代的话,每年可减少CO2排放量20亿t。而如果用目前最先进的燃煤技术取代美国现有的全部燃煤机组,CO2排放量可能每年将降低25%,也就是每年几乎5亿公吨的规模。
美国首个超超临界项目
美国最大的公用电力生产商和销售商之一的美国电力公司(AEP)认识到,需要继续发展新型燃煤发电技术,这样可以满足所在服务地区的预计负荷增长量。服务地区包括西阿肯色州和东德克萨斯州。为此,AEP公司于2008年11月开始兴建John W. Turk, Jr这一600MW纯燃煤电厂(TPP),同时AEP将USC技术引入美国。尽管负责供应USC电厂的供货商所提供的性能保证更具优势,但本项目仍将整体气化联合循环(IGCC)作为可探讨的备选方案。表1列出了AEP公司考虑采用的IGCC、亚临界及USC设计方案在CO2排放量上的细小差别。
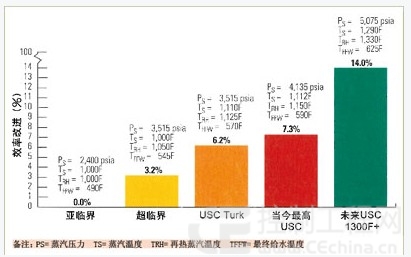
图4 与传统亚临界蒸汽发电厂设计方案相比,超超临界蒸汽工况将提升约6.2%的TPP电厂效率,并每年减少超过30万公吨的CO2排放量
采用USC技术的另一个关键衡量标准是效率情况。USC电厂是指在3500psia和1100F(593℃)以上工况下运行的电厂,而传统的超临界机组是在1000F~1050F(538℃~566℃)的蒸汽温度和最高3500psia的压力工况下运行。具体级别要求细致的设备配置决策。
TPP汽轮机的设计方案高效优化了蒸汽循环和运行参数,并采用最先进的材料确保在要求的压力和温度下可靠运行,为此还采用了一种焊制转子设计方案,保证该材料适合极端的运行环境。同时,也包括了新型高压(HP)和中压(IP)汽轮机设计。另外,还选中了一台配备直接氢冷转子、定子铁芯及水冷定子线圈额定功率为840MVA的Alstom Gigatop发电机。
紧凑可靠的配置
为TPP选定的USC汽轮机的构造属于一种冷凝式串联单再热3600rpm汽轮发电机组。经过验证的Alstom STF60设计方案是一种四缸式汽轮机,其中包括一台单流式HP汽轮机、一台双流式IP汽轮机和两台双流式下排气低压(LP)汽轮机。IP汽轮机通过连通管连接至LP汽轮机。整个汽轮机构造如图2所示。
在Alstom的标准设计方案中,HP汽轮机缸和IP汽轮机缸是分离的。而这种紧凑型的设计不易产生发生在某些联合HP/IP型汽轮机上的自激振动。由于在任何运行条件下,包括甩负荷和旁通运行条件,每个缸的轴向推力都是平衡的,所以发生在某些联合型HP/IP设计中的不平衡轴向推力现象也消失了。而且,因为蒸汽不会从HP与IP段的密封件处泄漏出去,所以分离式HP和IP设计的长期效率也较为卓著。
紧凑设计的缸体加上单轴承设计形成了较短的总轴长,并因此形成了更短的汽轮机。所有的汽轮机和发电机轴承均独立于缸体结构,并直接从基座获得支撑。这条设计原则,不但保证了轴的对中工作简便易行,也缩短了整个机组的安装时间,同时也确保了汽轮机发电机组长期稳定的运行特性。在TPP采用的设计方案中,入口阀门直接法兰需要安装至HP和IP缸体,这样就取消了汽轮机入口回路或连接管路,以此提高效率并加大可接近性和方便维护。
优化的蒸汽循环
以下是一些用于迅速确定USC工况优于亚临界汽轮机工况的经验法则:
主压力提升100psia,能将电厂净效率提升约0.16%。
提高主蒸汽温度10F,可将电厂效率提升0.16%。
提高再热蒸汽温度10F,可将电厂效率提升约0.13%。
最终给水温度每增加10F,可将电厂净效率提升约0.1%。
这些经济法则也存在一些应用上的限制。例如,通过提升蒸汽工况来提高效率的方式受可供采用的冶金技术和成本的限制。尽管如此,提升循环效率的关键还是尽量提高蒸汽温度。为TPP选择的最终优化蒸汽工况,如表2所示。
TPP设计是通过采用8个加热器来提高最终给水温度的方式来提高效率的,而传统的亚临界机组采用的是6~7个加热器。而且,TPP设计还采用了一个高于再热压力(HARP循环)加热器。另外,在下游采用了4级低压凝结水加热器,以及一个除氧器,还有3级高压给水加热器。从HP汽轮机蒸汽流道取一路抽汽用于供应最高的加热器。

表1 不同技术方案的CO2排放量。此表是AEP公司对John W.Turk,Jr电厂不同燃煤技术方案排放量的估算结果。本估算所采用的燃料为次烟煤。
HARP循环的一个重大优点,是其设计可以在没有再热器压力的情况下,优化最终给水温度,同时还可减少LP排汽湿度。在TPP中,采用了570 F的最终给水温度,这样即可以优化性能又能够遵守锅炉的运行条件。
TPP的优化蒸汽循环加热率保证值,以20%夏季、20%冬季和60%年平均工况为基础。循环示意图内的凝汽器压力代表了加热率保证值的平均工况。另外,TPP循环采用了一台100%负荷的单流式锅炉给水泵汽轮机,这台汽轮机完全集成到了主汽轮机系统之内。整个汽轮机系统由Alstom的数字控制系统进行控制。
由于蒸汽参数升高和最终给水温度提升,总功率为672MW的TPP运行效率,将比具有相近额定功率的新建亚临界机组高出大约6.2%。与新建亚临界汽轮机机组相比,这种效率上的提升相当于每年减少超过30万公吨CO2的排放量,以及在30年生命周期内减少超过1亿公吨CO2的排放量。根据 Alstom循环计算的各种循环参数对比,如图4所示。
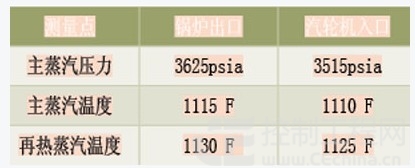
表2 AEP公司John W.Turk,Jr电厂的蒸汽工况。
Alstom自1957年以来,一直在从事超临界汽轮机的供应业务。Alstom的超临界机组如今已多达66台,总发电容量为44GW。这个数字包含了AEP和Tennessee Valley Authority的额定功率为1300MW的并列多缸机组。位于德国Lippendorf电厂的两台机组(各为930MW)是Alstom最大的单轴机组,这些机组1999年开始投入运行。目前有一个1100MW的单轴机组正在兴建中,其主蒸汽温度为1112F,再热至1148F。
材料上的重大进步
可靠汽轮机设计方案能在USC蒸汽工况下实现运行,其中最重要的原因是选择了正确的制造材料。针对这一方案,Alstom与其合作伙伴进行了大量的深入研究,围绕锻造、铸造、高蠕变破裂强度下的管道、脆化耐性、冶金学稳定性、低氧化速率、氧化层强度及制造难度等各个方面。在汽轮机内部,HP和IP转子、内缸、阀门缸体及入口叶片级均选用了先进材料,特别是采用了9%~12%的铬铁素体钢以保证运行上的灵活性。表3所示为TPP汽轮机设计方案所采用的具体材料。CB2材料用于铸造件,FB2材料也用于锻造件,这些材料均由COST 522计划开发。
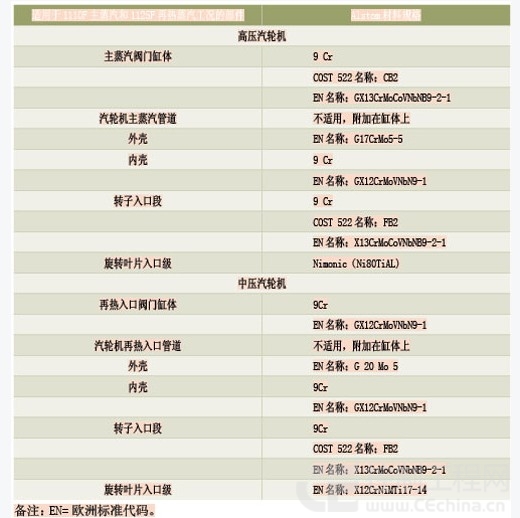
表3 AEP公司John W.Turk,Jr电厂的汽轮机材料。

图5所示,是从用于传统亚临界设计的X20钢种到当前欧洲正在开发的COST 536材料的进步过程。COST 536旨在开发适合下一代USC汽轮机使用的汽轮机材料。COST 501计划开发用于超过1130F(610℃)的材料,已经投入运行约10年时间。COST 522计划所开发的具有更高蠕变强度和更高氧化耐性的新型材料适用于高达1165F(630℃)的运行工况,而且已经很好地用于许多正在欧洲兴建的 Alstom USC汽轮机计划中(再热温度高达1148F/620℃)。
汽轮机设计特点
因为转子是由多个较小的锻造盘体构成,所以可在转子各段采用不同的材料,这样转子上特定级采用的材料就能够在相应工况条件下最准确地运行。TPP高压和中压入口转子段选择了FB2材料,这种材料是为实现更好的蠕变特性而开发的。与工作在相同工况下的整体转子相比,热瞬态期间的焊制转子应力水平可以降低多达40%。因此,与整体转子相比,Alstom的焊制转子具有一项额外的优势,能够实现更快速的启动和/或降低寿命消耗率。图6是在Alstom制造工厂拍摄的锻造盘体材料示例及焊接照片。
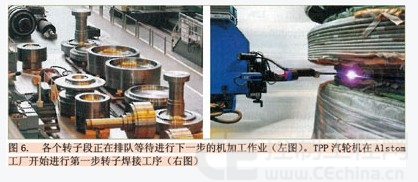
尤其在较高温度下,径向对称性应该是引起极大关注的事项。Alstom自20世纪60年代起,采用的HP汽轮机扣环设计成功地取消了内缸体螺栓法兰,从而最大程度地提高了径向对称性。相应的,因下部内缸体的应力减少了蠕变和变形,延长了机组使用寿命和被迫停机间歇期。由于内缸体处于对称压缩条件下,法兰设计可能产生的椭圆化现象并不会发生。此设计的优点是长期稳定的间隙和持久良好的效率。对于USC应用来说,这些优点可带来长期的可靠性和优异的运行灵活性。图7所示为一个装配到下半外壳前后带有转子的HP内缸。
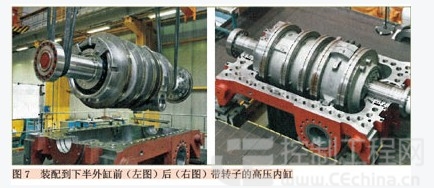
采用水平对分外缸和内缸的基本双壳体IP汽轮机设计方案属于常见方案,但也通过了审慎的材料选择来适应更高温度的USC工况。此外,IP汽轮机内缸经过改造,内壳部分采用了更为和谐的质量分布,以尽量减少在更高温度下入口部分的变形,其好处是可以长期保持不变的间隙和效率。
多种提升效率的设计方案
Alstom在HP和IP汽轮机上采用隔离缸体的设计原则,使蒸汽流道设计人员可根据USC机组较亚临界机组具有更长的膨胀线,优化汽轮机级数的完全自由度。与典型亚临界机组应用相比,HP汽轮机和IP汽轮机的级数增加了约25%。
TPP汽轮机性能在USC蒸汽工况下进行最大化的过程中,也考虑了其他设计参数。全弧形进口涡管在提高效率的同时,也最大可能减少了部件的热疲劳损坏。在此设计方案中,控制阀门在典型情况下全开运行,通过锅炉给水泵进行流量控制。过压运行提供了可在要求情况下产生额外电气输出功率的汽轮机流量裕量。
TPP汽轮机还计划配备Alstom最新开发的蒸汽流道和密封技术。Alstom始终坚持改进翼型设计,并通过减少间隙及与主流量相互作用的泄漏流量优化整个蒸汽流道,并考虑采用刷式密封件和耐磨涂层密封件以进一步提升效率。
排汽区在蒸汽循环效率中起到了关键性作用,因此优化最后一级的性能有着至关重要的意义。4英尺×72.1英尺的TPP排汽区,覆盖了各种设计环境条件下的运行范围。