自动控制技术在120 t转炉控制系统中的应用
发布时间:2009-11-03 作者:乔卫国,杨怀玲,孟伟,王永刚
当前国内120 t转炉主要还是依靠操作人员 的经验配合相关操作数据进行操作,人工进行终 点控制,命中率不到50%。由于往往要进行补吹, 因此严重地影响了生产效率和钢水质量。为提高 产品的质量和生产效率,莱芜钢铁集团有限公司 进行了120 t转炉自动炼钢的研究。[ 1 - 2 ]
1 研发思路及方案制定
转炉炼钢控制主要包括两个方面:过程控制和终点控制。过程控制主要是吹氧造渣操作,以 便使转炉炼钢过程得以平稳进行;终点控制则是 要求在吹炼终点时获得成分和温度都合格的定量 钢水。我们根据莱芜钢铁集团有限公司120 t转 炉的设备工艺和控制现状,按照全自动智能炼钢 的目标,制定了缜密的技术方案,以期达到智能化 炼钢的目标。
本系统的技术开发工作涉及氧压自适应控制、氧枪定位、氧步判断、天车物流跟踪等多个系 统的设计与开发,系统复杂,联锁条件多,控制及 安全要求严格。
通过本系统的开发,预期实现转炉系统的吹 氧操作(控制吹氧量和吹氧时间) 、枪位控制、冷却 剂操作(控制加料量和加料时间)的自动控制,实 现转炉炼钢生产各个流程的最优协同作业,实现 120 t转炉的全自动控制。
2 系统升级改造
莱钢120 t转炉原有自动化系统主要采用西 门子S72400系列控制器,为了实现全自动智能炼 钢控制,必须在原控制系统的基础上进行大幅度 的技术升级和设备改造。主要目的是完成生产过 程控制、数学模型的建立、生产指令的下达、生产 流程中各子系统的协同作业、数据采集、数据显 示、历史数据存储、故障报警和故障自诊断等功 能。
211 硬件
改造后的硬件系统包括: ( 1) 9 套西门子S72 400系列PLC,用于现场工艺控制与数据采集; (2) 1套S72400系列PLC,用作一级与二级系统之间 的网关; (3) 1套副枪数据采集与处理系统; ( 4) 1 套带有自定位、数据采集与处理的天车物流跟踪 系统; (5) 2台用于现场控制的一级热备服务器, 2 台用于二级数据处理系统的冷备服务器, 9台用于 现场控制的操作员机, 3台用于工艺控制的操作员 机, 1台用于工艺工程师的工程师站。
根据系统的结构特点、系统设备的分布情况、 稳定性和安全性要求,对整个网络系统的拓扑结 构进行了整体规划,整个网络分为控制系统的一 级网络和生产调度管理用的二级和三级网络。
一级系统各系统之间采用以太环网进行数据 通信,有效地保证了各控制器之间、控制器与上位 机、上位机之间的数据实时通信,不会因为网络中 某一个节点或者某一段光缆故障而影响系统之间 的正常数据传输,确保了生产的正常进行;并且当 某一个节点或某一处光缆出现故障时,网络本身 能够自动检测到出现故障的部位,提示维修人员 进行故障查找。
转炉二级网络采用的是星型网络,在主服务 器室设有主交换机,经过网关分别连接到副枪数 据采集、化验室质量分析等系统。一级和二级之 间经过Gateway进行数据交换,既保证了数据的快 速传输,也对一级控制网络和二级管理网络进行 了有效的安全隔离,对一级生产系统起到可靠的 安全保证。其网络示意图如图1所示。
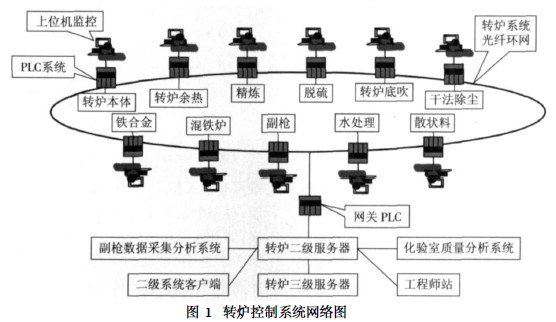
212 软件
在原有控制软件的基础上又增加了数据传 输、分析和处理软件,主要包括: (1)利用西门子的 WinCC V610 + SP3监控软件和Step 7V514编程软 件实现一级控制系统的适应性改造和升级; (2)化 验室质量采集与分析处理软件; ( 3)天车物流系 统软件; (4)副枪的数据分析与处理软件。
化验室质量分析系统软件用户界面如图2所 示,天车物流系统软件用户界面和副枪数据采集 与处理系统软件用户界面省略。
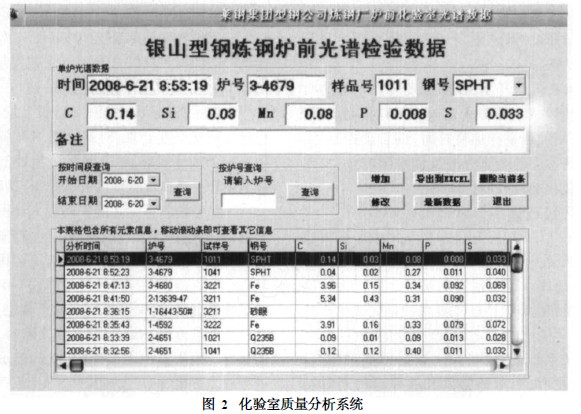
3 技术创新点
311 氧压无扰动自适应控制
氧压控制在智能炼钢控制中起着十分重要的 作用。氧气压力和流量直接影响钢水的质量、产 量、炉龄、成本等重要参数。提高氧气压力,也就 是提高氧气流量,将增加氧气对钢水的穿透能力, 提高反应强度,从而缩短吹氧时间,缩短冶炼周 期;但氧压过高又会造成喷溅,损坏炉衬,并且除 尘效果也非常差。尤其在莱钢120 t转炉系统中, 一次除尘采用的是LT干法除尘技术,开吹压力过 大会造成静电除尘器泄爆,损坏烟道、静电除尘 器,并容易引发事故; 而压力过低,不仅不好“点 火”,还会直接影响冶炼周期和钢水质量。因此, 如何控制好开吹氧压和过程氧压的平稳性就成了 重中之重。为此,我们将氧压控制过程分为两个 阶段(开吹氧压曲线如图3所示) ,第1个阶段是 从开吹到120 s,采用P ID控制,将氧压由开吹时的 013MPa上升到120 s时的0185MPa左右,这样控 制的主要目的是防止人为操作可能导致的干法除 尘系统泄爆,并且防止不易“点火”现象的出现。 第2个阶段是从120 s之后到吹炼结束,采用的是 二级系统的模型控制曲线,此时完全由二级系统 模型的计算结果给出流量设定值,并根据此设定 值进行流量控制。
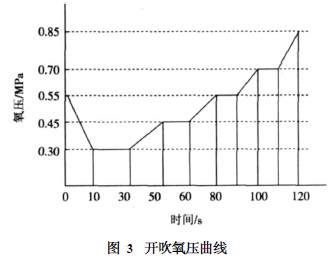
在氧压控制的这两个阶段的过程中,有几个难点非常关键,一个是氧气总管压力波动时的控 制,再一个是从第1 阶段到第2阶段的无扰动切 换,即开吹氧压曲线与二级模型曲线的无缝拟合, 第3个是手/自动的无扰动切换。任何环节如果 控制不好,都会导致氧气压力和流量的大幅波动, 直接影响到过程吹炼和加料控制的效果。为了解 决这些问题,我们采用了两种控制方法:一是快速 跟踪稳定法,二是差值计算跟踪法。快速跟踪稳 定法是针对总管压力波动的控制,采用了P ID控 制方法来实现在总管压力波动时阀后压力的稳 定;差值计算跟踪法是针对在开吹曲线与二级模 型曲线切换以及手/自动切换时的控制方法,其目 的是实现无扰切换,其方法是若切换时二级的氧压设定值与开吹氧压曲线的氧压结束值的差值在 允许范围内,则系统接收二级的氧压设定值;若差 值的绝对值偏大,系统将自动把氧压设定值修改 到差值范围之内,并给予10 s的调整时间,以使差 值控制在允许的范围以内再进行切换,避免系统 出现氧压较大幅值的扰动。
312 步进式氧枪精确定位
氧枪枪位控制不好,很容易导致喷溅或者返 干,甚至出现安全事故。在转炉炼钢智能控制中, 氧枪精确而快速的定位对整个冶炼过程起到举足 轻重的作用,为此,我们采用多种方法实现氧枪的 安全控制。
第一,采用双编码器技术,在每一个氧枪减速 机上安装两个增量型编码器,一方面进行氧枪位 置的测量,另一方面两个编码器互相进行校验。 当一个有问题时,就会发出报警信号,提示进行检 查。第二,采用了上下限极限控制和主令控制技 术,即使两个编码器全部出现问题,也会将氧枪控 制在要求的范围之内。第三,氧枪提升由西门子 变频器(型号: 6SE703620EK60)进行驱动,采用矢 量闭环控制,在参数设置中采取了紧急停车以及 断电保护等措施。第四,采用步进式差值跟踪方 式进行枪位的精确定位,将氧枪定位精度控制在 10 mm之内,并且可以防止氧枪的抖动,即当操作 工在操作画面上点击“开始吹炼”按钮后,在检测 到所有条件满足之后(包括编码器正常信号) ,氧 枪开始按照二级模型设定的枪位进行下降,此时 变频器的设定频率为35 Hz;当降到开吹氧位时, 氧阀打开,吹炼开始,此时,变频器的设定频率为 25 Hz;氧枪继续下降,当实际位置与设定值差值在 30 cm时,氧枪的速度进一步降低,变频器的设定 频率为15 Hz;当差值到10 cm时,变频器的设定频 率降低为5 Hz;当差值达到±2 cm以内时,氧枪停 止运动。反之亦然,在此不再叙述。
由于采取了差值跟踪的控制方式,配合氧枪 抱闸的控制,达到了氧枪控制既快速精确又防止 抖动发生的目的,最大限度地保证了生产安全,保 证了转炉炼钢的顺利进行。
313 基于Graph图形氧步判断的散状料加料
在转炉炼钢系统中散状料加料控制是一个非 常繁琐的控制。在每个氧步中,可能会有两个或 者更多的设备动作,这些设备或是进行称量,或是 进行投料。另外,每个称量斗对应1~4个高位料 仓,在这些高位料仓之中可能有2~3个料仓存储 的是同一种料。这样就需要解决几个问题: (1)各 高位料仓的料种判断; (2)判断加料次数以及所加 料是否与氧步对应; ( 3)判断料单是否发生变化, 如果发生了变化,则要重新进行氧步扫描,防止漏 掉氧步; (4)如果在当前氧步之中没有称到足够的 料,该如何处理。这一系列的问题使得散状料的 控制变得非常复杂和困难。为此采用了Graph图 形顺序控制软件进行氧步精确判断,并采用事件 触发的方式不断进行过程扫描。
散状料加料时,根据氧气用量累计判断当前 是第几次加料,给“步”赋值为当前步。在每一步 中都要调用自动振料控制和自动加料控制。程序 会根据“步”值来查询相应表单,以获得振料的重 量和打开哪个称量斗的扇形阀。
如果在规定时间内称量料斗不能放空,则系 统会自动转到备用料仓,并在监控画面提示操作 人员注意。在操作画面上还有实时的加料结果显 示,包括每一步的加料量和每一种料的累积量,既 方便操作工查看,又方便于报表的生成。
314 具有精确时效性的天车物流自动跟踪系统 各道工序天车的称重数据(废钢、铁水、钢水) 是转炉生产工艺数据的重要组成部分。现开发应 用的天车数据自动采集系统利用定位模块和无线 发送/接收装置,将加料跨、出钢跨的各天车数据 按炉次、时间实时采集处理后送入转炉二级系统, 为转炉的全过程自动控制提供了可靠的数据保 障。
在整个天车物流跟踪系统和二级系统中炉号 的对应是一个关键技术,如果对应错误就会导致 整个炉次的数据计算错误,导致模型计算失真,再 通过不断的自学习后,可能离实际的冶炼要求越 来越远,最终导致模型无法使用,所以如何实时实 现炉号对应非常关键。为了很好地解决这一问 题,我们采用了具备时效性的应答方式进行炉号 和数据的对应,即三级系统下达计划,二级系统接 收计划并将计划代码发送到物流跟踪系统。物流 跟踪系统接收到计划代码后将收到的信息反馈给 二级系统,二级确认反馈信息,最终实现双方对炉 号的确认。炉号确认后,在15 min内接收到的稳 定数据作为本炉次数据进入二级系统,二级系统 接收到数据以后,再发给物流跟踪系统,确认收到 后,双方本次通话完成。如果没有收到数据或者数据信息错误(如其值不在正常值范围内) ,或者 没有炉号,则系统会采纳默认值(正常范围以内的 值,并提示可以进行人工输入) 。当有新的计划下 达时,就会进行新一轮的校验,这样就避免了错误 数据的传送。这样做的优点是: (1)采用一体化组 合定位器,在每一个需要定位的工位,如转炉,出 钢线等,加坐标定位标识模块(行列式面定位方 式) ,自动跟踪天车,判断物料种类; ( 2)根据工艺 流程,自动进行数据统计; (3)多部天车,单计算机 管理; (4)无线通信,网络布局灵活; (5) CDMA通 信方式,节省频率资源; (6)时效性高; ( 7)数据传 输精确。
在采用了天车物流跟踪系统后,数据传送的 准确率大大提高,差错率由以前的210%下降到了 011%以下,为转炉智能炼钢的实现打下了坚实的 基础,并且大大降低了原材料的浪费。
4 结束语
自从2008年6月莱钢120 t转炉投入智能控 制后,最大的意义在于提高了终点双命中率,使得 补吹率大大降低,提高了生产节奏,冶炼周期平均 缩短了2 min,冷却剂加入量平均每炉钢减少600 kg以上,脱氧剂的加入量平均每炉钢节省20 kg以 上,钢水质量也有了大幅度提高, 在今后的研究工作中,需要对转炉炼钢的动 静态模型进行进一步的训练与优化,进一步提高 各个子系统的控制水平,不断完善一级系统以及 现场设备,进一步优化整个转炉区域的协调作业 能力,以期提高炼钢终点控制精度,达到更高的自 动控制水平。莱钢在120 t转炉上实现的基于副 枪的智能控制,对国内同等级别的转炉具有很好 的借鉴作用。
参考文献:
[ 1 ]龙 英,潘 恒. 基于全集成自动化平台的转炉控制系 统[ J ]. 冶金自动化, 2007, 31 (1) : 58260. LONG Ying, PAN Heng. BOF control system based on TIA p latfrom[ J ]. Metallurgical Industry Automation, 2007, 31 (1) : 58260.
[ 2 ]高卫立. 静、动态炼钢模型在济钢120 t转炉上的研究 和应用[ J ]. 冶金自动化, 2007, 31 (2) : 68