300t转炉底吹位置优化及其效果
发布时间:2009-10-29 作者:焦兴利,毛鸣,佟溥翘
马鞍山钢铁股份有限公司(以下简称马钢) “十一五”技术改造和结构调整重点工程———炼钢 连铸工程,在马钢新区建成了两座300 t 转炉和 与之相匹配的精炼连铸装置,年产567 万t 高档 汽车板钢、家电钢、双相钢、弹簧钢、管线钢等高附 加值产品。转炉采用顶底复合吹炼模式,透气元 件选用双环缝式元件,为了保证转炉底吹系统效 果,促进熔池冶金反应,减少终渣FeO 含量,降低 钢铁料消耗,我们通过对底吹位置优化的研究,确 认了合理的底吹位置。
1 转炉底吹特点
马钢四钢轧300 t 顶底复吹转炉,采用北京 钢铁研究总院专利产品———Φ22 mm 型双环缝式 底吹供气元件。每座转炉安装16 个双环缝式底 吹供气元件,每个供气元件有独立的气体流量自 动化调节、控制系统。底吹设备紧凑,设备费用 低,操作自动化,维护简单。底吹供气系统中,同 时配有空气吹堵系统,在底吹供气元件发生堵塞 现象时,可以采用高压空气进行吹堵复通处理。 转炉采用复吹工艺后,熔池搅拌均匀,同时能在较 大范围内调节底部供气强度,控制转炉内的搅拌 力,适合从低碳钢到高碳钢各种钢种的冶炼。通 过实行严格的底吹供气元件维护,能够在不更换 底吹元件的条件下,保持底吹供气元件寿命与炉 龄同步,达到长寿复吹的目的。
在吹炼前期采用氮气作为主搅拌气源,在吹 炼终点前5 min 切换为氩气搅拌,或根据氧含量, 能实现自动切换。底吹供气强度范围为0. 03 ~ 0. 10 m3 / (t·min) 。底吹供气模式前期变化不大, 后期需根据终点碳含量的变化改变供气强度。终 点碳越低,则底吹搅拌所需气量越大。根据终点 碳含量从低到高,控制系统中设定A、B、C、D、E、 F、G 7 种供气模式可供选择。
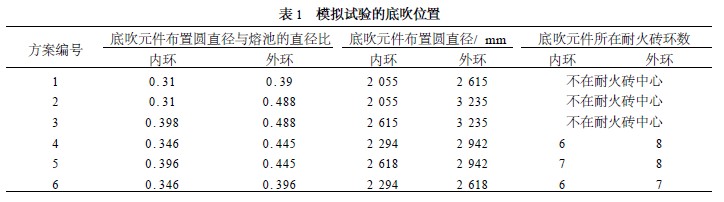
2 底吹元件位置优化
2. 1 底吹元件确定原则
借鉴同类转炉底吹位置布置经验,结合水模 冷态模拟试验,初步确定底吹供气元件的基本位 置;底吹元件位置应尽量避免布置在顶吹氧枪的 冲击圆范围附近,防止造成顶、底吹冲击能量相互 抵消,影响搅拌效果;底吹元件位置应是易于通过 溅渣及吹扫炉底等工艺,保持良好底吹元件蘑菇 头的形态;底吹供气元件应尽量布置于一环砖的 环中心位置处,以减少切砖量,便于转炉炉底砌 筑;避免底吹透气元件布置在副枪的下方,以减少 副枪粘渣,影响测量。
2. 2 水模试验
马钢300 t 转炉布置了16 支底吹透气元件,分 两环布置,为了确定合适的底吹透气元件位置,马 钢委托北京钢铁研究总院,进行过水模优化试验。 根据相似理论,进行复吹转炉流动混匀的物理模拟 时,要保证原型与模型的几何相似和动力相似,在 几何相似的前提下,保证原型与模型的修正弗鲁! 准数相等。水模试验供气参数由弗鲁! 数确定,供 气强度选定为0. 04 、0. 06 、0. 08 、0. 10 、0. 12 m3 / (t· min) ,根据耐火砖的环数分布情况,选择6 组方案 进行水模试验,见表1 。通过测量熔池混匀时间, 比较各底吹供气元件布置方案熔池混匀时间的长 短,优化出底吹供气元件布置方案。
试验将16 支底吹供气元件交叉布置于两个 同心圆上,通过模拟试验,测定了底吹供气元件布 置位置、供气强度对熔池混匀时间的影响情况,如 图1 所示。
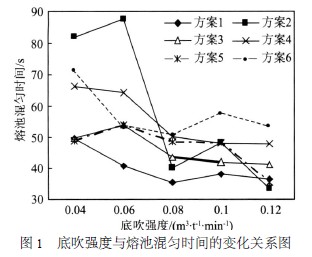
第1 组布置方案熔池混匀时间最短,效果最 好,但这种布置方式内环不在炉底砖中心,需调整 到0. 296倍(直径1 965 mm) ,这样内环底吹供气 元件距离氧枪最大冲击圆(1 601 mm) 只有182 mm ,容易造成顶、底吹冲击能量相互抵消。 第3 种布置方案熔池混匀效果其次,该方案 内环8 支底吹供气元件均布置在熔池直径的0 . 39 倍位置上,外环的8 支底吹供气元件均布置在熔 池直径0. 488倍位置上,但其外环底吹元件位置距 炉底边缘(炉底直径:5 036 mm) 只有900 mm ,极 易造成由于溅渣后炉底角部积渣,使底吹供气元 件上的渣层过厚,影响底吹的冶金效果。
第5 种布置方案,外环8 支底吹供气元件在熔 池直径的0. 396倍位置上,内环8 支底吹供气元件在 熔池直径的0. 445倍位置上,与第3 种布置方式比较, 底吹供气强度在0. 06 m3 / (t·min)以下时熔池混匀时 间基本相同,增大底吹供气强度时,熔池混匀时间比 第3 种布置方案长;当底吹供气强度在0. 12 m3 / (t· min)时,熔池混匀时间比第3 种布置方案更短。同 时底吹内环位置也处在氧枪最大冲击圆以外,距炉 底边缘的距离也相应增加到1 065 mm。
综合考虑顶、底吹和副枪位置及炉底砖砌筑 等因素的影响,底吹供气元件的炉底布置选择第 5 种方案,即外环8 支底吹供气元件布置在熔池 直径的0 . 396倍位置上(第8 环砖) ,内环8 支底吹 供气元件布置在熔池直径的0. 445倍位置上(第7 环砖) ,角度不变,较为合理。
3 吹炼效果
目前马钢四钢轧主要生产低碳钢种,图2 为 2 号炉的炉龄中期时200 炉终点碳和终点活性氧 对应关系图。转炉到吹炼终点时,使用贺利氏测 温、定氧和取样复合探头测量,钢水中活性氧直接 通过副枪测量出来,试样送化验室分析,图2 中钢 中碳来自化验室分析,活性氧直接测量获得。从 图中可以看出终点碳质量分数基本控制在 0. 015 %~0 . 10 %之间,活性氧质量分数分布在 0. 02 %~0. 10 % ,终点钢中C 和O 呈现明显的对 应关系,可以看出碳质量分数在低于0. 03 %时,活 性氧质量分数迅速升高,因此转炉终点碳质量分 数应大于0 . 03 % ,才能有效抑制终点高活化性渣 对炉衬的侵蚀,同时也能减少炉后合金消耗。图 3 显示了各炉次终点的[ %C]·[ %O ]值,从图3 可见,终点[ %C]·[ %O ]值基本分布在0. 001 5~ 0. 003 0 ,说明了终点[ %C] ·[ %O ] 平衡控制较 好,能有效防止吹炼低碳钢引起的过氧化。
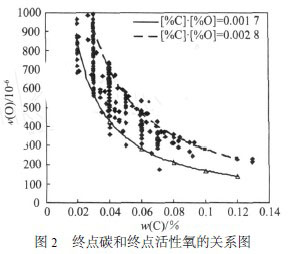
![200 炉次的终点[ %C]·[ %O]值直方图](http://www.cechina.cn/upload/article/6babecb0-9d23-4074-8426-8bb6cf711a2e/4.jpg)
4 转炉底吹的维护
低碳钢冶炼对转炉耐火材料侵蚀较为严重, 特别是马钢四钢轧300 t 转炉底吹元件较多,底 吹强度大,对炉底的侵蚀尤为严重。
为了减少炉底侵蚀,提高底吹透气元件寿命, 通过长时间的摸索改进,取得了较好的效果,主要 措施为:溅渣护炉时,加入轻烧白云石和碳粉调整 溅渣炉渣化学成分,保障渣中MgO 的含量,减少 渣中氧化铁和氧化亚铁含量;当炉底下降时,及时 调整加料模式,在前一炉溅渣结束后,将下一炉约 50 %的轻烧白云石和石灰加入到炉底,然后兑铁 水加废钢,减少铁水和废钢对转炉炉底的直接冲 击;采用激光测厚仪快速准确地测量炉底耐火层 厚度,及时调整转炉加料工艺和炉底护炉操作,保 证转炉炉底在合理的范围内。
马钢300 t 转炉第一个炉役已经超过5 500 炉,在炉役期内未修补底吹元件的情况下,实现了 底吹元件与炉龄同步。通过一年来生产实践,马 钢已经基本掌握了300 t 转炉底吹系统的维护和 长寿技术,吹炼过程平稳、喷溅少,容易化渣,可以 有效保证终点钢液内的C、O 平衡。
5 结 论
通过水模拟试验,对马钢两座转炉底吹透气元 件的位置进行优化,并综合考虑顶、副枪位置和转炉 砌筑,确定了转炉透气元件的位置,通过一年来生产 实践摸索基本掌握了300 t 转炉底吹系统维护和长 寿技术,确保在不更换底吹元件的情况下,底吹元件 与炉龄同步,同时取得了良好的冶金效果。