可靠性分析减少潜在的严重环境风险
发布时间:2009-10-16 来源:ABB评论
过去几年,不断提高可靠性日益成为一个重要的课题,所谓可靠性是指 一种产品、设备或流程,在特定的条件下和特定的时间内能够按计划运 行而不发生故障的概率。提高工厂的可靠性有利于减少流程和设备发生 故障时的费用并提高产量,从而获得更高的毛利率。此外,高可靠性还 能提高工作场所的安全性,减少潜在的严重环境风险。
今天,在竞争激烈的石油天然气行业中,天然气工厂必须实现高可靠性 的运行,从而不浪费任何资金或产生额外的费用。ABB 采取客观的量化 措施,帮助这些公司实现目标,将设备故障在早期就加以解决。本文将 列举三个特定的案例,介绍 MEGA 公司 (位于阿根廷 Loma La Lata) 推行 可靠性分析的具体情况,其成果就是节约!
有远见的组织都努力 追求零缺陷和零事 故。其中很多还将“零容 忍”原则应用于设备故障 管理, 实现零故障。然 而,实行设备自动化管理 最终也会出现问题。为 此,一些领先企业正在实 施两个重要的设备管理策 略:即根据设备状态进行 维护和可靠性实践分析。 其关键就是通过计划和调 度措施,对故障进行早期 预测及干预,实现对故障 的管理控制。
正如以下三个案例所显示的,可靠性 实践分析在这两项战略中作出了巨大 的贡献。第一个案例考核了液化天 然气 (NGL) 泵机械密封的可靠性分 析;第二个案例是验证了螺杆式压 缩机的改造;而第三个案例则对温 度变送器 (TT) 进行了可靠性分析。 MEGA —— ABB 全责绩效服务 (Full Service®) 的合作伙伴 作为 ABB 与 MEGA (位于阿根廷 Neuquén 的 Loma La Lata 地区的一家天然气厂) 签订的全责绩效服务 合同的一部分,ABB 负责机械、电 气、仪表和静态管理,以及负责静 态检验、计划和调度及零配件等材 料的全面管理。
要想真正参与全球竞争,企业 不仅需要很高的设备利用率, 而且可靠性也要高。因此选用 最佳管理方式尤为关键。
MEGA 工厂负责液化天然气的回收和 分离。这一流程是从液化天然气中分离出甲烷,然后注入管道 中,再供应给国内市场。其 它成分再通过管道输送到位 于 Bahia Blanca 地区的另一 家工厂做进一步加工。这是 一家液化天然气分馏工厂, 在这里将液化天然气分离成 乙烷、丙烷、丁烷和汽油, 然后销售给客户——即阿根 廷政府和 Bahia Blanca 工厂 (见图 1 )。
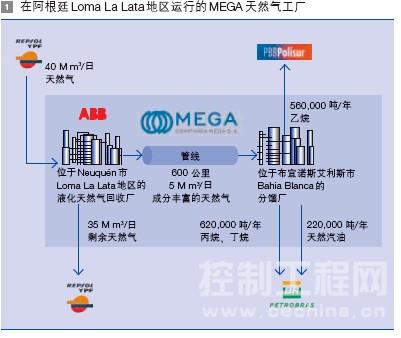
满足客户预期
设备利用率已接近世界一 流水平 (见图 2 )。然而,这一指标 也反映了流程中关键设备的利用 率,其中大部分为脱机备件或联机 备用设备。作为全责绩效服务的供 应商,ABB 希望提供最新的服务技 术和最先进的管理实践经验。因此 ABB 将重点放在其它的流程关键设 备,并根据市场需求,提高设备利 用率,使之与工厂运行同步。
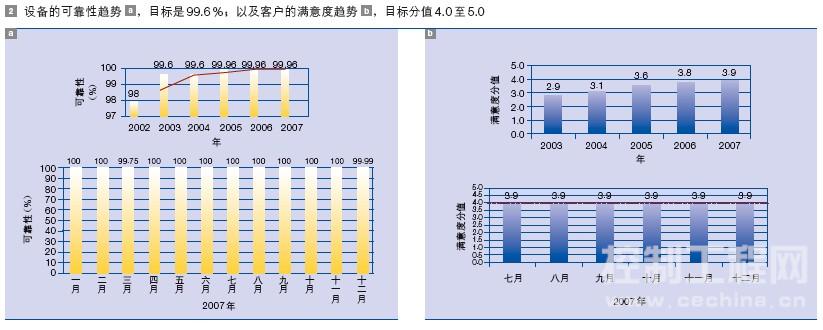
从辅助到实际行动
2008 年初,ABB 全责绩效服务年度 现场评估在 MEGA 完成。现场评估 认为初期效果很好,而且还识别出需要进一步改进的地方。每一项评 估都附有建议,协助 ABB 的现场工 作组尽可能缩小那些已经发现的绩 效差距。
虽然在 MEGA 进行的现场评估非常 有效,但显然还有提升空间,以提 高现场初期缩小质量和数量差距。 这意味着:实施以提高客户、ABB 和员工价值为目标的初期工作卓 有成效,反映了 ABB 全责绩效服 务的成效三角 (见图 3 )。这种做法 已被命名为“后评估辅助”法 (见 资料库 1 )。
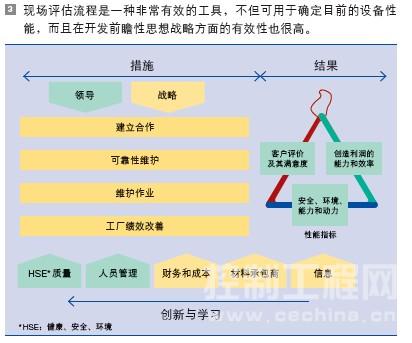
关键是通过计划和调度措施, 对故障进行早期预测及干预, 实现对故障的管理控制。
后评估辅助法开发了一条特殊通 道,成为每个现场独特的路线图。 它包含了目的地、目标和需要在现场 开展的初期工作,旨在缩小现场绩效 与客户期望值间的差距 (见图 4 )。
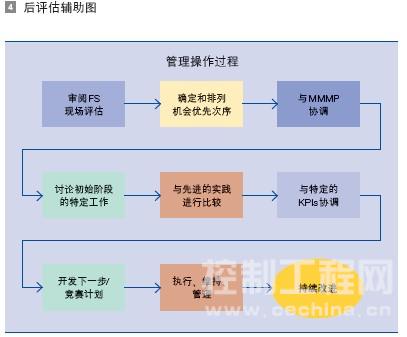
提高可靠性的做法
对于大多数个人而言,表现可靠性 的数据,无论是百分比、平均故障 间隔时间 (MTBF),还是几个书面紧 急指令,都缺乏任何改进的意义。 对于企业而言, 财务的可靠性问 题,意味着设备和流程故障的非可 靠成本控制,因为这类故障导致资 金浪费并影响生产能力。
从工程学的角度看,可靠性通常通 过对故障发生的机率进行量化确 定。计算概率时,涉及概率和统计 方法及相关工具的使用。天然气工 厂中典型的可靠性分析,包括不同 可靠性工具的使用,例如 Weibull (维泊尔) 分析、Pareto (帕累托) 分 析和 Monte Carlo (蒙特卡洛) 模拟分 析 (见 资料库 2 )。
可靠性分析的关键是工厂数据的质 量,因此如何获得这些数据、如何 管理、由谁负责分析至关重要。石 油和天然气行业大多数工厂已经积 累了多年的数据,但很难找到负责 分析这些数据的人员,以及能够用 于解决实际问题的信息。
设备的数据是显示工作状况的一个 最好手段, 也可以发现改进的机 会。通过检查故障的发生频率,确定 问题所在,然后开始分析,这是个 不错的方法。了解情况的第一个工 具是参考排在 Pareto 图表“前 10 位”数据。Pareto 分析主要用来排序 不同的机会,从而将重点集中于最 高价值的机会。80/20 规则表明,百 分之八十的问题或损失由百分之二 十的设备或流程造成 (见图 5 )。
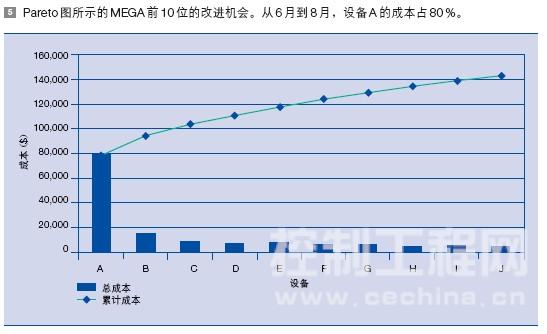
可靠性分析:液化天然气泵的机械 密封
根据 Pareto 分析,ABB 工程团队选 择分析了 510-P-01C 型液化天然气泵 可靠性。他们认为,由于流程条件 与原始设计条件不一致,泵系统的 可靠性较低。
天然气工厂中典型的可靠性 分析,包括不同可靠性工具 的使用,例如 Weibull 分析、 Pareto 分析和 Monte Carlo 模 拟分析。
其次,计算机维护管理系统 (CMMS) 数据库对 510-P-01C 型液化天然气泵 的搜索显示,最常见的故障模式与 机械密封的故障有关。
在可靠性专业领域,人们经常说, 维护管理根据故障模式进行。故障 模式是指在任何情况下,可能使一 种资产 (或系统、或工艺) 造成故障 的任何事件。因此,故障模式会导 致资产功能的丧失。常见的故障模 式为:轴承卡死、叶轮卡住、电机 烧坏和吸气管线堵塞。
液化天然气泵是生产流程的关键设 备,将已加工的产品输送到 Bahia Blanca 工厂,在这里分馏成其它产品 (乙烷、丙烷和丁烷)。根据从液化天 然气泵采集的 CMMS 数据,应选择 具备 Weibull 分析能力的可靠性应用 软件。用于计算可靠性的方程式如 下:
Rt = e - ( – ) β , t > 0 t η
式中:
R (t) = 可靠性数值 (0 ~ 1)
t = 故障时间 (小时、周期)
η= 比例参数 (小时、周期)
β= 形状参数 (β<1;β=1;β>1)
从 CMMS 数据库中采集的数据如图 6 所示。Weibull 分析法揭示了故 障模式的结果,其具体的描述如图 7 所示。
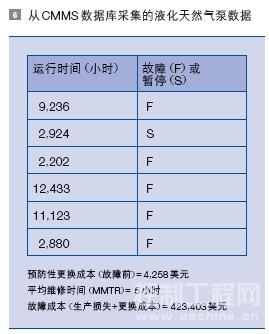
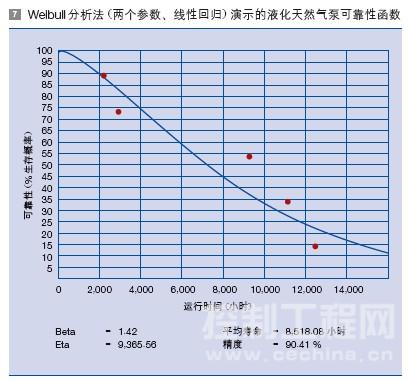
采用 Weibull 分析法的一个优点是: 它提供了一个灵活的制模方式,其 中包括早期生命模式、随机模式和 磨损故障模式。就机械密封而言, 其平均故障间隔时间为 8,518 小时, 这表明,50 % 的机械型泵密封尚未 运行 8,518 小时,就已发生故障。 而 50 % 的故障发生在运行 8,518 小时 后。这一分析告诉客户,必须提高 机械密封的性能,更新泵系统。
再次,ABB 团队进行了成本分析, 以确定更换备件 (机械密封) 的最佳 时机。图 8 显示更换机械密封的最 佳时间大约在运行 650 小时,这样每 小时运行可节约 103 美元。然而, 这样的更换频率似乎并不现实,因 此,ABB 团队按照不同的运行时 段,分析可能的更换时间。
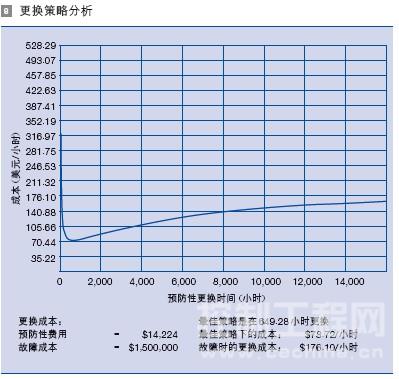
运行 4,000 小时后所作的第二次分析 表明,每小时运行可节约 66 美元。 然后,他们在运行 6,000 小时后又做 了第三次分析,证明每小时可节约 46 美元。最后,运行 8,000 小时后的 第四次分析显示,每小时可节约 36 美元。
根据 Weibull 法的分析结果,ABB 团队提出几项建议。经过慎重考 虑,MEGA和 ABB 同意重新设计或 进行修改, 在定期更换的基础之 上,执行维修策略。双方确定安装 一套有利于机械密封的增压系统 (见图 9 )。
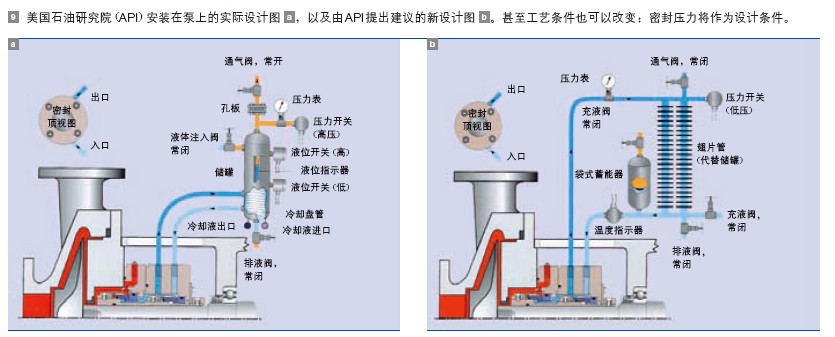
80/20 规则表明,百分之八十 的问题或损失由百分之二十的 设备或流程造成。
改造 (每台泵两个密封) 费用约为 90,000 美元。改造以后的产品可靠 性,采用 Weibull 法的数据分析进行 监控,可将 MTBF 延长超过原先制定 的基准,从而判定其可靠性的改善 情况。
螺杆式压缩机的 Weibull 分析 螺杆式空气压缩机被列为流程关键 设备。压缩机的功能是通过压缩空 气为设备的仪表供油。如果不提供 压缩空气,工厂内的仪表系统将会 失灵,导致读数错误,使生产控制 发生变化,空气压缩机因此被列为 关键设备。
有些意外的故障发生在电阻温度检 测仪 (RTD) 的传感器。RTD 是测量压缩空气热度释放的检测装置,如 果它发生故障,螺杆式压缩机就会 停止运行。对发生故障的根本原因 进行分析 (RCFA) 之后,ABB 团队断 定:主要故障模式由压缩机运行中 的剧烈振动造成。
然后,他们设计了一种减振装置来 减少故障 (见图 10 11 )。但仍然存 在如下问题:通过改造能减少振动 模式故障机率和提高可靠性吗?
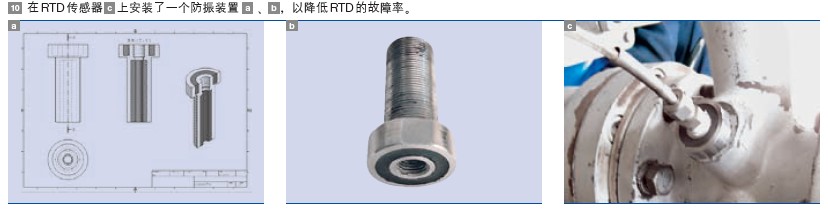
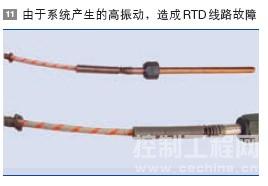
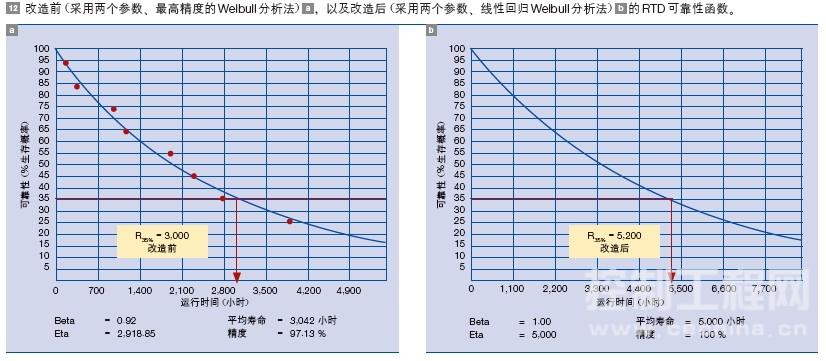
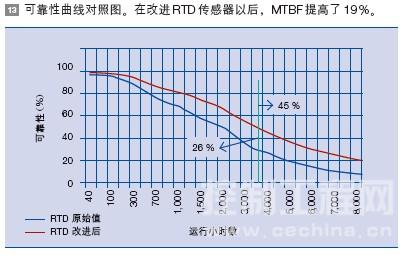
Weibull 分析法可以评估可靠性的改 善程度。
根据事先修改的 3,042 小时 MTBF 和 事后修改的 5,000 小时 MTBF,实际 改善大约为 2,000 小时,MTBF 约提 高了 19 % (见图 12 13 )。ABB 团队将 继续监测 MTBF 的改进,并着手解决 下一个主要故障模式。
温度变送器的可靠性分析 在敏感的自动化控制中,温度变送 器 (TTs) 控制流程中的温度。由于过 去几年频繁出现故障,因此选用了 这一控制设备。随机出现的故障 (即 没有明显的故障模式) 使提高可靠性 面临很大的挑战。
Weibull 分析法提供了一个灵 活的制模方式,其中包括早期 生命模式、随机模式和磨损故 障模式。
ABB 团队从 CMMS 设备的历史资料 中收集了所有的故障数据,旨在进 行可靠性分析。发送给 TT 的故障数 据是 2001 年至 2008 年期间从 CMMS 系统中采集的。此后,他们采用可 靠性应用工具,创建了一个可靠性 曲线模型,以确定各种故障模式 (见 图 14 )。
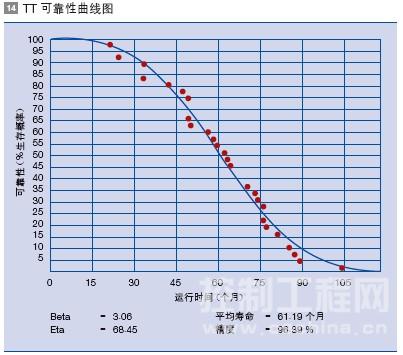
简单绘制的数据表产生了一些令 人惊讶的效果。MTBF的计算花费 了 61 个月,相当于 5 年。工业中其他的类似设备,典型的 MTBF 为 25年至 150 年。
ABB 团队在一个实验室中, 对类似的设备做了进一步 的数据分析和测试。最后确 定,问题实际上出在仪表系 统内部,而根本原因在于原 始设备制造商 (OEM) 的设 计。这一分析引起了 MEGA 与其 OEM 之间的一场讨 论,导致 MEGA 因以前的 TT 设备故障而收到了一笔 信贷,而且还给 OEM 提供 数据,以创建一个新的改良 版本。
高可靠性意味着高优先权 为确保业务和应对世界金融 危机,各企业之间竞争激 烈,迫使他们努力探索降低 运行成本的各种方法。一个 流行的做法就是削减设备的 维护费用。然而,这是一种 非常短视的做法,因为延缓 投资往往会造成非常严重 的后果,可能会使费用增加 2 倍至 5 倍,除非他们能够在故障发展的早 期加以解决。
数据分析导致 MEGA 因以前 的 TT 设备故障而收到了一笔 信贷, 而且还给 OEM 提供 数据,以创建一个新的改良 版本。
设备的及时维护及随后的可靠性改 善不但可降低设备缺乏可靠性的整 体成本, 也可降低相关流程的整 体成本。同时, 这种做法将能改 善业务绩效和创造更多的利润,增 加有效生产时间或利用率, 提高生产能力。此外,更高的产量将弥 补设备的额外投资,从而降低维护 费用。
延缓投资往往会造成严重的后 果,可能会使费用增加 2 至 5 倍,除非能够在故障发展的早 期加以解决。
各种战略和工具已准备就绪,可用 于协助选择对设备的最好维护策略 以及更换决策。作出这些决定旨在 确定采取什么样的维护策略,以保 持系统的功能。特别是利用以可靠 性为基础的具备 Weibull 功能的应用 软件,可以提高客观的决策能力。
要想真正参与全球环境下的 竞争,企业不仅要求提高设 备利用率,而且可靠性也要 高。在了解应采取什么样的 设备管理策略以后,就可以 迎接新的挑战,选择预维修 更换部件的最佳间隔时间、 检修频率、基于设备状况的 维修计划、主要设备的更换 方案,以及维修资源的需 求。选择最佳的维修方法, 可以增加实现低运营成本、 提高可靠性和利用率的可能 性,以确保更可靠的生产。 这一最佳方法可提高人们的 积极性,大大提升为客户、 人员和 ABB 创造的价值。