MES国内外发展情况分析
发布时间:2009-09-16 来源:www.cechina.cn
MES的发展历史
计算机辅助生产管理系统的演化历史如下图所示,MES作为生产形态变革的产物,其起源来自工厂的内部需求。

上个世纪八十年代,MRPII在美国生产与库存管理协会(APICS)大力宣传和组织推动下得到了迅速的普及和广泛应用。推广过程中,MRP II也暴露出一些不足之处,如MRP II对预测需求和销售管理不够重视,对车间的大量实时事件与数据不能很好地利用等等。
许多企业认识到,需要其它系统来解决MRPII在这些方面管理薄弱的问题。于是,为了满足销售、预测的需求,产生了分销资源计划DPR(Distribution Resource Planning)。同样,为了强化车间的执行功能,制造执行系统(MES)也就应运而生。
传统的MES(Traditional MES,T-MES)大致可分为两大类:
1)专用MES系统(Point MES)
它主要是针对某个特定领域的问题而开发的系统,如车间维护、生产监控、有限能力调度或是SCADA等。
2)集成MES系统(Integrated MES)
该类系统起初是针对一个特定的、规范化的环境而设计的,目前已拓展到许多领域,如航空、装配、半导体、食品和卫生等行业,在功能上它已实现了与上层事务处理和下层实时控制系统的集成。
虽然专用MES能够为某一特定环境提供最好的性能,却常常难以与其它应用系统集成。专用的MES整个系统重构性能弱,很难随业务过程的变化而进行功能配置和动态改变。集成的MES,比专用MES迈进了一大步,具有很多优点:如单一的逻辑数据库、系统内部具有良好的集成性、统一的数据模型等等。
AMR研究小组在分析信息技术的发展和MES应用前景的基础上,提出了可集成MES(Integratable MES,I-MES)这一概念。它将模块化和组件技术应用到MES的系统开发中,是两类传统MES系统的结合。
从表现形式上看,I-MES具有专用MES系统的特点,即I-MES中的部分功能可以作为可重用组件单独销售。同时,它又具有集成MES的特点,即能实现上下两层之间的集成。此外,I-MES还能实现客户化、可重构、可扩展和互操作等特性,能方便地实现不同厂商之间的集成和原有系统的保护以及即插即用(P&P)等功能。
到90年代,MES发展为I-MES(集成MES)和MES-Ⅱ(Manufacturing Execution Solutions)。这样MES则作为整个工厂生产现场的集成系统出现,故又称为Integrated MES(E-MES)。主要功能为工厂管理(资源管理、调度管理、维护管理)、工厂工艺设计(文档管理、标准管理、过程优化)、过程管理(回路监督控制、数据采集)和质量管理(SQC-统计质量管理、LIMS-实验室信息管理系统)。在这个模型指导下,MES在90年代初期的重点是生产现场信息的整合。对于离散工业(discrete manufacturing)和流程工业(process manufacturing)来说,MES有许多差异。就离散MES而言,由于其多品种、小批量、混合生产模式,如果只是依靠人工提高效率是有限的。而MES则担当了整合、支持现场工人的技能和智慧,充分发挥制造资源效率的功能。
90年代中期,又提出了MES标准化和功能组件化、模块化的思路。这时,许多MES软件实现了组件化,也方便了集成和整合,这样用户根据需要就可以灵活快速地构建自己的MES。
从1997年开始的国际仪表学会(ISA)启动的编制ISASP95企业控制系统集成标准和ISA SP98批量控制标准的工作尤为重要,2000年发布了SP95.01模型与术语标准,2001年发布了SP95.02对象模型属性标准,2002年发布了SP95.03制造信息活动模型(Activity Models)标准,2003年发布了SP95.04制造操作对象模型标准。其中SP95.01已经被IEC/ISO接受为国际标准。SP95.01规定了生产过程涉及的所有资源信息及其数据结构和表达信息关联的方法。
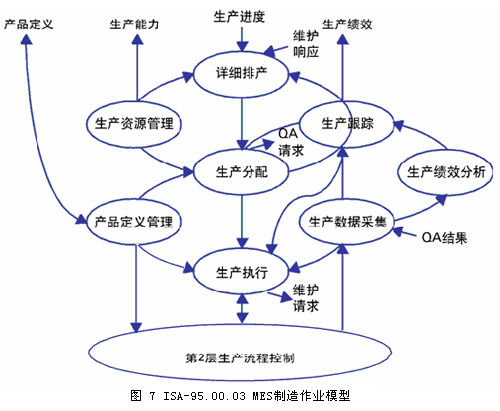
SP95.02对第1部分定义的内容作了详细规定和解释,SP95.03提出了管理层与制造层间信息交换的协议和格式。
2004年,全球批量控制论坛(WBF: World Batch forum)发布了基于XML技术的制造标记语言(B2MML)第二版。该标记语言旨在通过使用现有的软件行业标准,并在满足实时绩效管理(RPM: real-time performance)的前提下,显著地降低企业应用系统和生产系统集成的成本。在过去的两年里,基于B2MML技术的成果十分显著。基于B2MML技术的MES产品借助XML的灵活性、扩展性,能够使MES与ERP等其它商用系统的集成成本更低、更迅速。
MES在我国的发展
虽然MES的发展历史比MRPII、CAD、CAM都要短,但它能有效地实现“以时间为关键”的制造思想,因而在发达国家推广非常迅速,并给工厂带来了巨大的经济效益。MES的出现以及普及,对国外的管理界也产生了深远的影响。
近十多年来,我国通过863 CIMS项目应用的研究和推广,大大提高了企业的竞争力,使我国的制造业水平上了一个崭新的台阶。但是,我国制造业水平与发达国家相比还有较大的差距。
在工厂自动化FA(Factory Automation)方面,我国的制造业企业过去多是强调物流自动化,如自动化生产设备、自动化检测仪器、自动化物流运输存储设备等等。虽然它们能取代不少人工劳动并解决了一些生产瓶颈,但由于缺少相应的信息集成系统,这些系统不能充分发挥其功效而形成所谓的“自动化孤岛”。
制造业水平的提高,不单是采用设备自动化,提高生产管理信息系统的效率显得更为重要。在我国,MRPII、ERP已逐渐趋于成熟与普及,而面向制造执行层的MES软件在开发与应用方面还比较薄弱。
随着企业信息化应用水平的不断提高,企业逐渐认识到实现企业计划层与车间执行层的双向信息流交互,通过连续信息流来实现企业信息全集成,是提高企业敏捷性的一个重要因素。
因此,通过MES来实现企业信息的全集成,形成实时化的ERP、MES、SFC是提高企业整体管理水平的关键,这对企业制造业整体水平的提升具有重要意义。
“十五”期间,国家863项目研究,将MES作为重点研究课题,流程工业领域MES成为技术研究的突破口。
流程工业最突出的特点是,生产线自动化程度高,制造过程的信息已经取得,具备了信息数据基础,MES的重要性充分显现出来,企业对MES产生了迫切需求,流程工业MES实施条件基本成熟。由此,在2001年,国家863/CIMS主题将流程工业中,钢铁、石化行业的MES技术和应用的研究作为重点项目立项,下达了首批研究课题,最终目标是获得MES技术研究成果、形成系统、实现产品的工程应用。
2005年,由上海宝信软件公司联合清华大学、浙江大学、上海交大、东北大学、大连理工、冶金自动化院等六家研究院校共同承担的国家863计划“冶金工业MES架构和关键技术研究与示范应用” 课题攻克了冶金企业实际生产中的动态优化调度技术、网络环境下物流管理与控制技术、面向决策和操作的全面质量管理技术、生产全过程的动态成本控制技术、设备故障监测与评价分析技术、数据分析与挖掘技术、冶金过程流程模拟技术、结构化MES软件产品的设计、开发与系统集成等重大关键技术,提出了符合我国国情并具有国际先进水平的钢铁制造业MES控制策略与产品构架,制定出了行业推荐标准《企业信息化技术规范 制造执行系统(MES)》。基于该标准,开发完成了我国首套“冶金工业MES软件”产品,填补了国内流程工业MES领域内的一项空白,并在国内市场上与外国最先进的MES软件供应商的竞争中,以技术、价格等综合优势取得了绝对的胜利。在上海一钢公司、上海益昌薄板公司、马钢、涟钢、邯郸钢铁、包头钢铁、吉林通钢及梅山公司等等也都得到了成功的应用。此外,除了在这些钢铁行业以外,宝信的MES现已延伸到了金属和铝等其他行业。
而石化行业的排头兵中石化2004年开发出了具有自主知识产权、符合我们中国石化企业特色的中国石化MES系统,称为S-MESV1.0版,已经通过了863专家组评审通过,现在已经在发挥作用。
目前,我国MES开发的产品主要是软件供应商、企业自主开发、企业与科研院所共同开发几种主要的研究开发途径。其中软件供应商有大致可以分为六个方面:
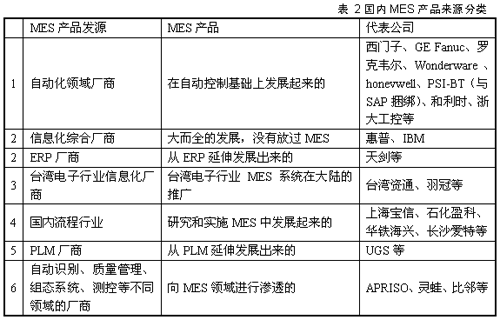
在MES产品的发展过程中,行业的需求对于国产MES有着很大的促进作用。譬如,在对MES需求最迫切的钢铁和石化行业,催生了国产MES系统做得比较理想的宝信和石化盈科公司。
近几年我国MES的研究和产业都有了比较大的发展,但是,国内MES的研究开发和技术应用仍然与国外有相当大差距,主要表现在以下两个方面:
● MES中很主要的内容是生产过程管理,其中必然要涉及生产计划,包括产品的质量计划、消耗计划、成本计划等等,这些计划最终通过调度指令、生产活动。过程优化问题是我国MES研究中的弱项。
● MES的智能化,也是我国MES研究开发与国外有差距的一个方面。过去,生产过程管理,凭借管理人员和操作人员的经验,我国MES系统仅仅提供了一个替代经验管理方式的操作系统平台,但是,如何将生产管理者的经验固化在MES系统中,在我国MES研究开发中还没有涉及。MES智能化是未来我国MES实现跨越发展的主要方向。