冗余技术在分布式控制系统中的应用
发布时间:2009-08-12 来源:www.cechina.cn
引言
在现代工业的各个领域,出于对高可靠性和安全性的考虑,及停车成本高或系统维护导致停产损失大的考虑,大都采用冗余结构来构建控制系统。
1、冗余DCS 系统
某酒厂的稻谷加工DCS 控制系统主要分为六个工艺段:进料、初清、清理、砻谷、碾米、出料等工段。所涉及的电气、仪表输入输出点数为6400 点,控制点数为576 点,由一个中央控制室集中控制。整套DCS 系统以西门子公司冗余组件为核心,由2 台S7-400 控制器、2台OSM 交换机、9 台ET200M IO 站、一台操作员站和一台工程师站构成。系统全部采用S7-400的高性能卡件,实现了供电模块、CPU、通讯介质、接口模块和客户机冗余。
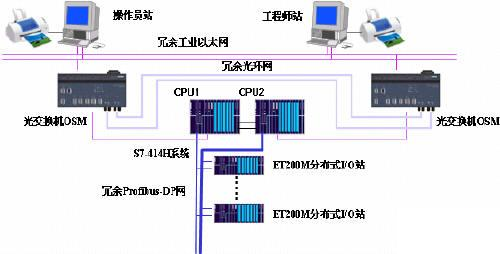
图1 冗余系统结构图
2、PLC 冗余
2.1 PLC 冗余的实现原理
两个CPU414-4H 是冗余系统的核心组件,以双通道结构进行操作,冗余的实现方式为“硬冗余”,冗余的切换方式为“热冗余”。冗余状态下主备CPU 具有相同的用户程序,并通过西门子专利的“事件驱动的同步”方法同步执行程序。一旦可能导致主备站的内部单元状态不同的事件发生时,例如对I/O 直接访问的事件,将由操作系统自动同步它们的数据。
冗余系统在正常状态下,主备CPU 同时参与程序处理和数据运算,不同之处是备CPU不输出控制信号。如果发生主站故障将进行无扰动主备CPU 切换,从中断点处由备CPU 接替生产过程的控制,并处于单机工作状态。CPU 无切换时间,系统切换时间主要取决于Profibus-DP 的切换时间,该段时间内输出保持切换前的输出状态,切换期间无信息或报警/中断丢失。对于其它公司的同类产品,一般CPU 切换时间达到毫秒级,只要切换时间小于I/O 延迟时间和报警/中断检测时间,便可以保证在切换期间无信号丢失。
2.2 PLC 冗余的可靠性论证
下面运用可靠性理论对系统的冗余设计进行可靠性分析,可靠性指标如下:

平均故障时间:指系统相邻故障期间的正常工作时间的平均值,用MTBF 表示。
失效率:指能工作到某个时间的系统,在连续单位时间内发生故障的比例,即瞬时故障率,用λ (t) 表示。
可靠度:指系统无故障正常工作状态的概率,用R(t) 表示,即R(t) = P(X > t) ,它是规定时间t 的函数,规定时间越长R(t) 越小。可靠度具有如下性质:
根据可靠性指标,对主控制器系统进行可靠性分析。设X 是主控制器系统能正常使用的期限,即从开始使用到第一次故障为止的时间间隔。则X 是随机变量,设它的分布函数为Fm(t) ,分布密度函数为fm(t) ,可靠度为Rm(t) ,则有: Rm(t) =1-Fm(t)。
考虑到电子产品和控制设备的失效分布大致都服从指数分布,即X 服从参数为λ 的指数分布,则有:
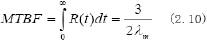
设λm为主控制器的失效率,根据定义
,结合式(2.1)(2.2)(2.3)可以得到
根据定义
,根据可靠度R(t) 性质②,得到
。结合式(2.3)(2.4)得到 
以上为主控制器单独工作时对系统的可靠性分析,下面对主备控制器组成冗余系统的可靠性进行分析。设R(t) 为冗余控制器系统可靠度,MTBF 为冗余控制器系统平均故障时间。
下标为s 的参数,定义为备控制器相对于主控制器相同类型的参数指标。
由于主备控制器为同种类型产品,并且工作负担基本一致,则有:
由于主备控制器为并联结构,并且可以看作为相互独立的概率事件,结合式(2.3)(2.7)
则有:
结合式(2.9)则有: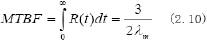
结论:通过式(2.10)和式(2.5)比较,发现冗余控制器系统的平均故障时间是单控制器系统的1.5 倍,即冗余控制器系统平均使用寿命是单控制器系统平均使用寿命的1.5 倍。
3、通信冗余
整个系统网络分为上层管理网和下层控制网,上层管理网由两块光交换机OSM 构成环网主架,每个OSM 向上由标准电缆,链接操作员站和工程师站中的一个工业以太网通讯卡CP1613。向下由标准电缆,链接冗余机架中的一个以太网通讯模块CP443,构成冗余工业以太网。通过ISO 传输协议和S7 通信服务实现操作站、工程师站和中央控制器间的数据交换。
下层控制网由西门子Profibus 专用电缆,加双路IM153 构成冗余Profibus-DP 网,向上链接CPU414-4H 的DP 口,向下链接ET200M 分布式I/O 站,完成对现场信号的采集、处理。
3.1 冗余工业以太网的实现原理
冗余系统与上位机监控的管理网是采用在双路冗余连接的基础上,通过光纤构成环网的连接方式。就双路冗余连接而言,其实质是为主备CPU 分别设计了一条独立的通信线路,通过上位机端配置的软件“S7-RedConnect”监视冗余连接状态,并在CPU 切换时,协助WinCC自动切换到新的主CPU 通信线路上来。可以看出这并不是真正意义上的冗余,如图2-a 所示,当总线0 通信线路处于工作状态,CP1613(0)出现故障时,通信随之中断。为了解决这个问题,在双路冗余连接的基础上,将两块光交换机OSM 互连,进行光纤环拓扑。改造后的通信线路如图2-b 所示,当出现同样的故障后,可通过光纤环网,经CP1613(1)继续维持通信线路的畅通。这样改造的好处是:在不改变原硬件接线的基础上,仅增加了两条光纤互连交换机,并且不需要任何硬件组态和用户编程,网络组态时,仅需要按照双路冗余连接进行配置,便可以实现当活动线路出现故障时,自动切换至备用线路。

图2-a 双路冗余连接

图2-b 冗余环网连接
3.2 冗余工业以太网的组态
S7-400H 系统与上位机通讯时,只能使用ISO 传输协议和S7 通信服务。所以用 STEP 7组态控制器的以太网通讯模块CP443 时,取消TCP/IP 协议,指定MAC 地址并激活容错连接的快速切换标志。组态两个PC 站时,分别禁止相应的工业以太网通讯卡CP1613 的TCP/IP地址并指定MAC 地址。在工业以太网上的每个节点配置好基本参数后,便可以通过NetPro工具,完成对网络系统容错连接的配置。但是这种配置实现的只是双路冗余连接,要想实现冗余环网,只需将两个交换机通过光纤互连,无需任何编程和组态。同时用NetPro 工具生成的通讯配置,以XDB 文件形式存放在PC 机上,该文件包含了PC 机所需的特定信息,如站点地址、使用的网卡等等,供WinCC 站使用。
为了实现上位机监控的目的,除了上面对冗余工业以太网的组态和参数设置外,还要求PC 机中安装“S7-RedConnect”。它在PC 机后台运行,负责监视PLC 冗余连接状态,并在检测到发生PLC 切换事件时,上位机端能够及时切换到相应的工业以太网通讯卡CP1613 上,保持上位机监控的有效性。此外,还需要在上位机端配置WinCC,它是西门子公司在自动化领域最先进的技术与微软公司共同开发的居于世界领先地位的视窗控制中心软件。具体配置步骤为:首先设置WinCC 站的PG/PC 接口,即将STEP7(NetPro)生成的通讯配置XDB 文件链接到该接口中;接着安装驱动“SIMATIC S7 Protocol Suite”,实现上位机端的S7 通信服务,及建立冗余通信通道;最后为冗余通信通道指定连接,该连接的程序名和连接名在通讯配置XDB 文件中指定。通过上面一系列的配置和参数设置,便可以成功的将S7-400H 系统连接到WinCC 站。
4、软件编程技术
采用西门子WinCC 作为上位机监控组态软件,针对两条稻谷加工生产线共设计了25 幅监控画面和若干重要设备工艺参数设定画面、重要工艺指标报表画面。设计时充分考虑了便于监控操作的科学性和合理性,主监控画面以子工艺段为单位,显示子工艺段的运行信息、故障信息、运行模式信息和总控面板。对各子工艺段的控制可由主控面板切换至该段监控画面,进行单动或自动控制。当重要工艺指标超限时,还将在当前监控画面出现即时报警提示并生成报警记录。
采用西门子STEP7 作为下位机编程软件,宏观上整个控制系统为典型的顺序过程控制,但是控制设备多、工艺流程长直接导致了连锁关系复杂;系统的分段分级控制直接导致了控制方式多变;现场环境差,随机产生的假信号导致对故障事件处理的复杂化,所以编程时需要充分考虑程序设计的合理性。
实际编程中为便于编程和调试采用了以下方法:
①将整个工艺分成若干子工艺段,并为每个子工艺段创建FC 块,以便于分段调试。
②为每个子工艺段的FC 块,构建相应的DB 块。用DB 块中申请的变量作为FC 块中逻辑运算的中间点,并为DB 块和块中的变量定义形象的符号名和相关注释。这样不仅可以在子工艺段调试和编程时,方便得检索、删除、增加和修改所涉及的变量,而且这些都是在使用
M 区时所不具备的优点。还可以避免使用M 区时,最容易出现的编译可以通过,但M 点却重复使用的错误。
③构建有通用功能的FB 块,如顺序控制功能块、模拟量处理功能块、故障检测功能块等,不但可以提高编程时的工作效率,而且可以在相应的DB 块中保存重要的过程数据。冗余PLC 执行指令的时间与标准PLC 执行同一指令的时间相比,效率基本降低了一倍,所以优化程序对冗余系统很重要。由于该工艺对时间响应确定性的要求不高,即对PLC 扫描周期的时间间隔确定性要求不高,可以将部分程序转入其它中断执行,使得该段代码仅在中断事件发生时执行。如果将这些代码完全放置在OB1 中执行,那么每个扫描周期将执行一次,将会花费大量不必要的程序扫描时间。实际编程中,将仅作为监测的模拟量处理模块放置时间中断OB32 中,中断为每1S 触发一次。将具有通用功能的断轴检测模块放置时间中断OB35中,中断为每500ms 触发一次。这样有效减少了不必要的模拟量处理和故障检测次数。此外该工艺需要使用大量定时器。但是CPU414-4H 中,S7 定时器仅256 个,远远不能满足工艺要求。实际编程中通过调用读取系统时间函数SFC64,编写顺序启停控制功能块FB,解决S7 定时器数量不够的问题。
结束语
该冗余系统不但提高了系统工作的可靠性,减轻了员工的劳动强度,而且提高了企业的管理水平。同时为方便以后系统扩容及改造,从硬件选型和编程结构设计方面都给予了充分的考虑。该系统已交付使用,至今运行良好。
本文作者创新点:将冗余技术应用于落后的粮食加工工业,并提出了一套可行的硬件设计方案;将双路冗余工业以太网改造成冗余环网,进一步提高可靠性;设计了一套在复杂工艺编程时,便于调试的程序结构设计的若干方法。
经济效益:该冗余系统可以保证稻谷加工全天运行,每个车间最大可以日产大米500 吨左右。根据该酒厂技改部负责人介绍与当初收购大米相比,按每天加工100 吨大米计算,从原材料差价、耗电量、人工费、维修费等综合因素考虑每天可以节约1.5 万元左右。这不包括米糠、糠壳等副产品的价值,和生产规模扩大后增加的酿酒成品的经济效益。
该项目从2005-10 月开始设计,2006 年春节后开始动工,2006-9 月试车,2006-10 月验收,至今运行良好。