带钢热连轧生产线自动控制系统
发布时间:2009-07-23 来源:www.cechina.cn
0 前言
凌源钢铁公司880mm中宽带热连轧机生产线是1992年开始建设的。这是国内首次完全依靠自己的技术力量为中宽带热连轧机设计和配套的自动控制系统并取得良好效果的工程项目。该套轧机原来是德国Krupp公司Leverkusen工厂1956年建造的,1993年拆迁到我国凌源钢铁公司,在工艺设备布置方面做了必要的修改。主要电气控制系统全部由国内配套,厂房是利用旧厂房扩建的,在较短的时间内投产见效,为凌钢增产创效奠定了基础。
冶金部自动化研究院在建设过程中承担了全部电气控制系统新设备的设计配套和利旧设备的修配改工作,在同类生产线建设中具有典型意义。本文主要以该工程的实施过程为例,介绍热连轧生产线自动控制系统的基本结构、硬件软件配置、控制功能、系统测试和现场调试等方面的内容,为以后类似工程提供借鉴。
1 工艺简介
该套生产线改造后,形成了较为典型的3/4连轧模式,总装机容量37000kW,年产50万t热轧板卷。其工艺设备包含4个部分:加热炉区、粗轧区、精轧区、卷取区。如图1所示。

加热炉为推钢式加热炉,由上料台、炉体、回料车、取钢机等设备组成。
粗轧区主要由1架立辊轧机(E1)、电动压下的四辊可逆粗轧机(R1)、前后侧导板、二辊单向粗轧机(R2)、双工位热卷箱(CB)、飞剪(SH)以及辊道组成。
精轧区主要由1架立辊轧机(E2)、电动压下的四辊精轧机(F1,F2,F3,F4,F5,F6)、活套装置(H1,H2,H3,H4,H5)、导卫装置等组成。
卷取区主要由2套夹送辊、地下卷取机(DC1,DC2)、废品卷取机、卸卷机、运输链等组成。
工艺过程为:来料150mm厚、7500mm长的连铸坯,经加热炉加热后,由R1轧制5~7道次,再经R2轧制1道次,成为16~25mm的中间坯,由热卷箱卷起保温,开卷后头尾对调,进入精轧机组轧制6道次,成为2~6mm薄板,经喷水冷却后,由卷取机卷成带卷。
2 控制系统配置
2.1 系统模式
60年代以来,带钢热连轧机的自动化不断发展,已经形成了功能齐全、技术成熟、效果显著的计算机自动控制系统。根据生产的需要,该套轧制线的电气控制系统按3个层次进行配置,分别为:操作站系统、自动控制系统、电气传动及检测仪表系统。各部分的控制功能都是由应用软件实现的,驻留在各个控制子系统中。各部分的控制信息通过计算机网络传递。层次结构如图2所示。

这是1个典型的基础自动化控制系统,其核心为1级的自动控制系统,它完成全部的控制功能,协调整个生产过程;0级的传动系统和仪表系统以及其他气动和液动设备作为执行机构,完成能量转换,驱动机械设备;2级的操作站系统作为人机界面设备,完成生产过程的设定、监控、统计等任务。工程师站主要用于工程技术人员定期对控制系统进行必要的维护和技术培训等,生产过程中,工程师站可在线也可离线工作。由这3部分构成了1个完整的控制系统,完成整个生产线的协调自动控制,而每层又都分成若干个子系统,完成相应的控制任务。
这种控制系统模式,既实用,又经济,为大多数用户所接受,也是目前国内中小企业普遍采用的模式。
2.2 硬件系统
根据生产的需要和生产中各工艺设备之间的运行逻辑关系,整个生产线的电气控制系统分2段进行构造:粗轧段和精轧卷取段。2段系统之间既彼此独立,又相互联系,协调工作,分述如下。
2.2.1 粗轧段
粗轧段的硬件系统由1套操作站系统和6套可编程序控制器系统构成。操作站系统为新系统,由IBM-7537工业控制微机为主配置而成;可编程序控制器系统分为3部分:R1轧机的速度控制和压下控制分别由A-B公司的PLC5/40L新系统构成,R2的控制系统和热卷箱的控制系统分别由3台SIEMENS公司的S5130A旧系统构成,飞剪控制系统由A-B公司的SLC500新系统构成,新系统由1条A-BDHplus网络连为一体。新旧系统之间信息交换通过硬件I/O进行。如图3所示。
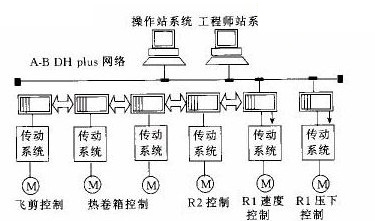
2.2.2 精轧卷取段
精轧卷取段的硬件系统由2套操作站系统和6套可编程序控制器系统构成,全部为新系统,分别完成精轧机的速度、压下、活套和1#卷取机、2#卷取机以及喷水冷却控制功能。操作站系统由IBM-7537工业控制微机为主配置而成;可编程序控制器系统均由A-B公司的PLC5/40L新系统为主配置而成,由1条A-BDHplus网络连为一体。传动系统由模拟U2系统构成,通过硬件I/O与自动化系统接口。如图4所示。
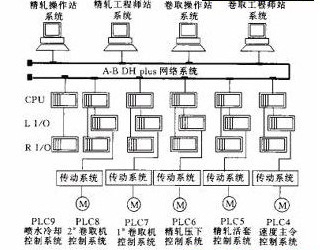
2.3 软件系统
软件系统分为2部分:系统软件和应用软件。
操作站系统的系统软件主要由WINDOWS操作系统和A-BCONTROLVIEW画面软件平台以及C语言系统构成;可编程序控制器的系统软件为A-B6203编程软件,以梯形图方式开发应用软件,它具有强大的算术、浮点和逻辑运算功能,编程清晰方便;网络系统选用A-BDHplus网络系统配置。
应用软件系统亦分为2部分:系统软件和应用软件。系统软件是指控制设备生产厂家为控制系统运行而设计的监控、总线管理、数据管理等基本软件或软件平台。应用软件是系统集成者满足某一特定用户的具体控制要求而设计的控制功能软件或软件模块。
操作站画面、报表系统的应用软件除少部分由C语言编制而成外,大部分都是由CONTROLVIEW系统配置的设定、操作、报警、报表等画面。生产过程中,操作人员只需在画面上通过功能键和数字键简单操作即可完成生产过程的设定等任务。画面的结构为树状结构,切换原则是:同一根下的同级画面可直接切换,不同分支上的画面要经过相应的根才能切换。
可编程序控制器系统的应用软件系统主要是实现生产过程的功能控制,通过梯形图语言逐条编制而成,采用模块化结构设计,清晰、易读、易维护。程序模块分为通用模块和独立模块,都驻留在相应的控制系统中,各模块之间的组织关系由主控程序管理。其主控程序结构如图5所示。
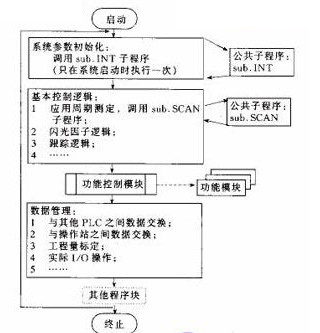
在软件模块设计时,大量采用了成熟的控制原理和控制算法,采用条件控制和时序控制相结合的方式,以有效利用系统能力资源和适应现场具体情况。操作方式为手动、半自动、自动等3种方式,在轧钢前可由操作人员根据设备状况自由选择。而轧钢过程中,只能按由高级到低级的顺序降级选择。程序设计中充分考虑了设备的安全因素和操作人员对生产过程的适当干预能力。
3 基本控制功能
控制系统的全部功能都是通过软件实现的,由驻留在各子系统中的功能模块完成,具体分解如下。
3.1 初轧区
初轧区控制系统的主要控制功能有:整个区域的速度设定、协调和控制;E1轧机和侧导板的开口度设定与控制;R1、R2轧机压下系统和位置设定与控制;R1制止道次设定、判别与控制;高压水除鳞控制;热卷箱的卷取、带尾定位和开卷控制;飞剪的定位、切头和切尾控制;粗轧区操作逻辑;粗轧区辅助系统联锁;粗轧区正常停车与紧急停车控制;粗轧区故障报警和打印;粗轧生产过程监控;粗轧生产参数设定与打印;粗轧生产报表的生成、显示和打印。
3.2 精轧区
精轧区控制系统的主要控制功能有:整个区域的速度设定、协调和控制;E2轧机的开口度设定与控制;F1、F2、F3、F4、F5、F6轧机压下系统的位置设定与控制;精轧机的AGC(预留);H1、H2、H3、H4、H5活套的高度、张力以及起落控制;活套控制自适应;高压水除鳞控制;精轧区操作逻辑;精轧区辅助系统联锁;精轧区正常停车与紧急停车控制;精轧区故障报警和打印;精轧生产过程的监控;精轧生产参数设定、存储与打印;精轧生产报表的生成、显示、存储和打印。
3.3 卷取区
卷取区控制系统的主要控制功能有:整个区域的速度设定、协调和控制;喷水冷却系统的控制;1#和2#卷取机的卷筒及其助卷辊控制;1#和2#夹送辊的控制;1#和2#卷取机的张力卷取过程控制;卸卷和带卷运输链的控制;卷取区操作逻辑;卷取区辅助系统联锁;卷取区正常停车与紧急停车控制;卷取故障报警和打印;卷取生产过程监控;卷取参数设定、存储与打印;生产报表的生成、显示、存储和打印。
4 系统调试和投运
该系统设计和制造完成之后,在实验室里进行了模拟调试和测试,称为实验室调试,分2个阶段:单体测试和系统联调。单体测试的主要任务是以模拟方式单个运行子系统,纠正硬件和软件中的错误,调整不合适的控制方式。然后,对系统施加适当的设定信号,模拟相应的反馈值,记录系统输出结果,对应用软件模块进行“黑箱”测试,分析控制趋势,检查各种参数是否基本合适。系统联调的主要任务是检查整个控制系统的工作状况,包括系统网络运行状态、各子系统之间的协调关系,各种数据流向等方面。在实验室调试完成后,要对系统的各个方面进行详细的记录和备份,以便到现场系统恢复时使用。
系统在现场安装完成后,进行了必要的系统恢复和现场调试。系统恢复是指将系统重新恢复到实验室系统联调完成时的状态,不同的是用现场实际信号取代实验室的模拟信号。
现场调试包括:单体试车、联动试车、负荷试车3个阶段。单体试车是指在相应系统的控制下单个运行考核每个工艺设备,必要时还要限时考核,如大电机及减速箱的8h联合考核。联动试车是指在整个系统的控制下按照生产要求运行考核某个区域或全线的全部工艺设备,发现问题,解决问题,直至满足生产需要。负荷试车是指用真实的原料去检查生产线能否生产出合格的产品。以上试车工作完成后,只能说系统基本具备生产条件,而系统的动态参数优化和控制精调指标还要在试生产中逐步调整和完善,直至达到全部合同要求,最后验收。
5 结论
该中宽带钢热连轧生产线的自动控制系统经过实验室的模拟测试和调试,经过现场安装后负荷调试,一次试车成功,最后顺利投产。经过2年多时间的试生产,满足生产要求,在1998年底,控制系统全面通过运行验收考核。
但由于建设时的资金问题,该生产线上投入的设备和系统都不够完善,现存的缺陷直接影响着成品带钢的质量和产量,亟待解决。主要有3点:
(1)R2轧机和热卷箱的控制系统仍然采用在国外已经使用了很多年的旧系统,已到故障率高发期,并且备品备件严重不足,影响产量,需尽快改造。
(2)精轧机的压下电机为旧设备,功率太小,不能调速且不能负载启动,因而,带钢在精轧机中没有厚度控制手段共分柿渴艿胶艽笙拗啤K淙辉诳刂葡低成杓剖蔽狝GC功能留有接口,但也只能在工艺设备改造后,才能考虑厚度自动控制问题。
(3)目前利旧的卷取机是非常落后的九辊助卷的卷取机,设备复杂,维护困难,故障率高,也影响着产量和质量的提高。
将来,若要进一步发挥这条生产线的作用,以上三方面就是下一步改造的重点所在。