机器人双雄记
发布时间:2009-04-27 作者:Lawrence D. Maloney
在被认作是对美国工人威胁的时候,机器人便一发不可收拾,迅速成为美国工厂正常运转的必须的生产力工具。
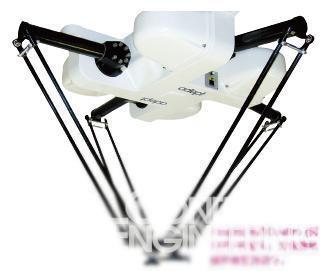
根据机器人工业协会的数据,近年来最大的增长之一是北美机器人公司在2007 年接受的订单提升了25%。现在这个行业增长到了一个阶段,在全美工厂里已经有大约178,000 个机器人在工作,这样美国成为仅次于日本的第二大机器人制造国。
虽然不同的机器人设计和目的相差甚远,但工程专家们说机器人系统有一点是相同的:他们是机电一体化设计的测试温床。开发机器人的工程师们,在将设计付诸于实践的之前,将各种不同学科的技术融合起来,并利用了最新的建模以及模拟工具。美国Design News 杂志社在采访了两家最前沿的机器人公司Adept Technologies 公司以及Motoman 公司之后发现,这种方法显然被用于了机器人设备的研究上。

Adept Technology:西方最快的机器人
Adept Technologies 公司位于美国加利佛尼亚州Livermore 市,他们在视频监控机器人设计方面赢得了全球声誉。从组装和测试到生命科学和医学领域,机器人设计同位于英国的 Prosurgics 公司合作开发了下一代机器人外科手术系统。在今年早些时候,Adept Technologies 公司取得了一个里程碑式的业绩,一次将25,000 个机器人成品下线运出。
就潜在的应用优势来说, 公司设计的新型机器人Quattro(得尤其显眼,因为它能够满足高于一切的客户要求:速度。“Quattro 机器人的性能是普通机器人的两倍。”Adept 总裁John Dulchinos 来说。“可以让客户在相同的厂房大小区域内生产的产品数量是原来的两倍。”
Adept 公司设计的Quattro 机器人是用于快速包装以及材料处理领域的,例如包装机器、纸板箱、托盘以及盒子的装载,以及传送带到传送带的传输。机器人具有集成视频和追踪功能,能够以180 个每分钟的速度从运动的传送带上夹取零部件。
就像项目经理Matt Bjork 指出的那样,Quattro 机器人在直径1.3m 的工作间以及2kg 的有效载荷内,用它一场快速的循环时间满足了市场的需求。他说,市场上SCARA 以及其他6 轴机器人通常有它们接触不到的“死点”。之前类似的机器人有效载荷超过0.5kg,它们在工作间的边角地区也表现不佳。
带固定四轴的Quattro 机器人一般被安装在1到4个传送带上的固定的框架里。它所具有的视频监控系统锁定传送带上运动的零件,然后通过传送带夹取追踪窗口,机器人决定什么时候拾起零件。
据工程师主管Jeff Baird 所说,机器人还可以被用于拾取从熔炉里出来随意摆放的小甜点。机器人首先熟悉传送带上的小甜点位置,然后在封装之前将它们拾起放置到第二条传送带的托盘上。
找到创新解决方案
为了实现Quattro 机器人野心勃勃的性能目标,设计小组需要解决机器人外部手臂和装载平台上的负荷的高压力。“为了迎合我们的设计标准,不得不测量G 作用力的大小并保证材料的疲劳强度超过5 亿个工作周期。”机械工程师主管Daniel Norboe 指出。“我们做了额外大量的研究找寻和描述对材料的需求以及设计的要求。”
在这些考虑要素中,设计小组需要使机器人的运动出错率降到最低,并保证重型电机和齿轮不受运动链系的影响。于是设计小组选择了如碳纤维这样的轻型材料制造机器人连接部件。结果是设计非常坚固,没有结构上的松动。另外,Quattro 机器人的加速度为15m/s2,穿过一般长时间运动中心的最高速度为10m/s。
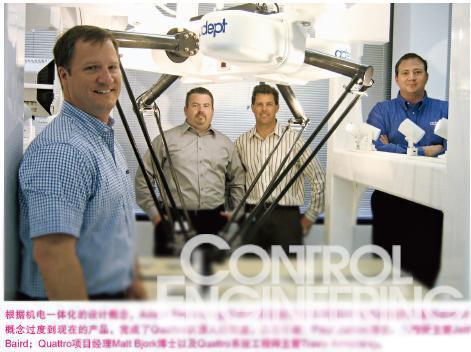
Quattro 机器人还安装了能够360度旋转的钟型机械装置。该设备安装在机器人的移动平台上,解决了与类似机器人设计中的旋转可靠性相关的机械设计问题。项目经理Bjork 用基础的数学方程式解释了有四个独立电机和手臂的机器人。数学与机械设计的结合,在凸缘平行时(没有任何倾斜的),可以让机器人的独立关节运动起来。由于要进行平滑线性工具的凸缘运动,所有四个关节必须由实时控制系统联系起来。四个独立的传动装置提供了四种不同的自由度:X/Y/Z 位置以及Theta 零件旋转。
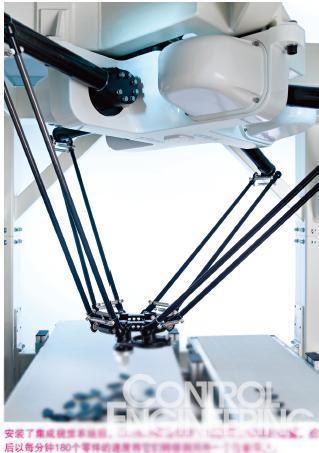
另一个机械设计的要求是机器人必须防水密封,在封装肉类和鱼之后, 能够用水清洗。所有外部表面能够经受食品类加工的腐蚀性清洗剂以及任何磨损颗粒。在ISO6 或者高级别更高的无尘室里,机器人外壳需要涂上新型涂层,因为机体多孔,会导致材料疲劳易脆。
同时,电子工程师解决了在压缩电子包内将高速和加速度结合后的精确定位。据公司电子工程师主管DeronJackson 所说,Adept 公司原来为公司的Cobra 机器人所设计的高性能“基础放大器”(AIB)技术,能够对问题做出正确的回答。
AIB 安装在机器人的基座上, 同Adept 公司的压缩智能控制器CX 硬件配合工作,来运行行业认可的V+ 软件。控制器采用Adept 公司智能伺服分配结构,能够协调多个Quattro 机器人一起工作。客户通过以太网能够将多个智能控制器连接在一起,组成任意大小的集成机器人生产线。整体生产线决定了对Quattro 机器人接口的要求。一些生产系统宁愿通过现场总线技术数码I/O 来配合工作,如DeviceNet;另外一些生产线利用客户开发的PC 接口或PLC 结构来连接机器人。为了减轻这些接口的负担,Adept 公司提供了像Adept ePLC 连接器或Adept 包装控制器这些设备。
Quattro 机器人系统设计主管TravisArmstrong 说, 在视频控制功能方面,Adept 公司在PC 平台(AdeptSightTM)或者智能摄像头技术基础上,设计了智能控制器CX。里面内嵌了大容量视觉存储库。视觉存储库采用了先进的视觉操作技术以及如目标定位这样的功能。目标定位功能是通过轮廓识别工具来定位零部件。Adept 公司还支持第三方视觉硬件,比如IEEE1394, 线性扫描以及千兆以太网摄像头。
“Adept 公司将运动和视觉控制紧密结合,让客户能够在任何时间和任何传输速度中进行零部件精确定位以及追踪。”
机电一体化以及更多
根据Adept 公司工程总监Baird 所说,混合了各个工程学科开发的Quattro机器人也许是项目最为简单的部分。“机电一体化是Adept 公司所采用的工程设计方法。”他说道,“我们提供的产品总是包含了机械设计、电子设计、内嵌软件、先进伺服/ 运动控制以及应用软件工具等解决方案。”
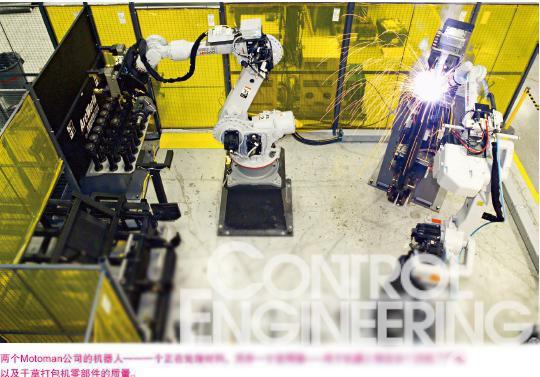
除了采用各种工程学科相互配合之外,Quattro 机器人设计小组还是用了许多软件工具。运动学家Paul James 回忆道,这其中最有价值的工具是Adept数码工作间。3-D 模拟和离线编程软件包使设计在与硬件结合之前最优化。例如,软件帮助解决了如Quattro 机器人向前运动的问题,这包括机器人工具的选择。数学计算涉及到了重复计算以及一元四次方程的解答。在使用Adept 智能控制CX 来实践之前,工程师们通过数码工作间对公式进行拓展、模拟以及测试。
机械小组采用SolidWorks CAD 软件来设计整个3D 机器人,使其能够完全呈现出来,并进行封闭研究。该软件也帮助决定机器人基座内电机和驱动链的正确位置。另外,FEA 工具,例如ANSYS和COSMOS,决定了材料的疲劳寿命。
“ANSYS 以及COSMOS 分析了机器人所有关键区域的硬度和压力。”机械工程师Norboe 说道,“例如,为了使平台重量更轻,我们在平台内分析压力大小,看平台是否足够坚固能够应付Quattro机器人在惊人加速度和高速下产生的高压力。”
最终目标:让客户满意
Quattro 机器人设计成果是设计小组进度表节奏紧张的来源。“我们从基本设计概念和大学的一些研究入手。”项目经理Bjork 说道。“三个月之后,我们对机器人80% 的部分都进行重新设计,并制造出原型。”
Adept 公司在一次展览会上展出了Quattro 机器人的原型,机器人在工作间内以引入注目的加速度和高速滚动撞球。然后他们开始了更多的验证测试以及对原始设计第二次反复设计。总得来说,从设计概念到第一个产品问世,项目足足花了9 个月。“只有各个学科高技术工程师们紧密合作,减少设计重复以及漫长的决定过程,才能达到的惊人的成果。”Bjork 说道。
简单的来说,Bjork 补充道,Quattro机器人的试运作阶段在公司的历史上是最快的一次。在最开始的9 个月里就销售出了200 台Quattro 机器人。早期的客户有食品、消费品以及制药公司。在三月份,位于德国的Solar line Saxony 公司选择了该系统安装到太阳能电池生产线上。“我们选择Adept 公司以及Quattro机器人是因为他们能够帮助我们实现史无前例的生产目标。”SLS 公司总裁Karsten Barth 说。
Motoman 公司的机器人:他们是良好的团队合作者在世界上所有机器人制造公司里,只有Motoman 公司是最多产的。作为日本Yaskawa 电子公司的一家子公司,Motoman 公司的生产线能够提供超过175 个机器人模型,以及40 种工程解决方案。
位于美国俄亥俄州Dayton 市附近Motoman 公司的总部,拥有能够设计、建造以及集成自定义机器人系统的应用和项目工程设计小组。这些机器人能够做的工作有:
●在测试实验室里每小时可分类950个血样管。
● 23 秒内清除挤压的铝制部件。
●将自动过滤器装载到货盘上,每分钟16 箱。
Motoman 公司的工程师越来越多地设计出能容纳2 个或者更多机器人的工作间——这是机器人行业的被称为“合作机器人”的一种趋势。
为位于美国宾夕法尼亚州的NewHolland Agriculture 公司所设计的材料处理和焊接系统就是例子之一。农场设备制造商需要 新型焊接技术,来处理18种不同的干草打包机滚轮组装。这些零部件每个都包含了两头带耳轴的管道,需要先进行定位间断焊,其次是塞焊,最后是端口接缝处的环形焊。零部件是由6.0-6.6mm 厚的ASTMA500 型钢制成。
虽然这些组装生产线之前安装的焊接系统也采用了机器人,但零部件需要采用传统的焊接方法,手动装载、卸载和夹取。在更小直径的材料卷上焊接到位尤其困难。操作者需要100% 检查焊接组装材料,然后按要求将卷曲的材料弄直。甚至这样,那些没有对准焊接的零部件最后被研磨或者手动修补焊接点。如果没有发觉,为对准的焊接会导致机器振动,这些是机器磨损以及现场潜在焊接缺陷的直接原因。
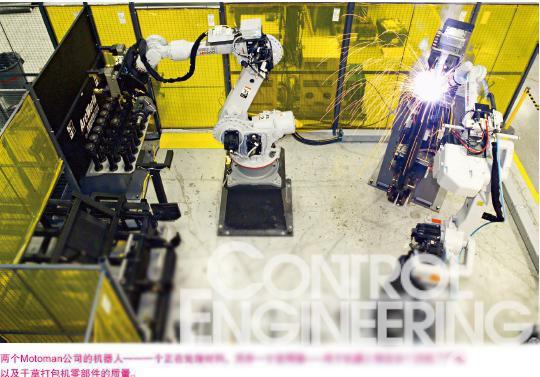
同Motoman 公司的工程师一起,NewHolland 公司用新型、安装了两个机器人全自动工作间解决了问题。装载和卸载机械滑动物体的MotomanHP200 材料处理机器人, 被安装在机头座的定位器上, 由Motoman HP50 来进行弧焊。在降低了装卸货物人力的同时,该系统可以满足2小时无人看管生产的需求,并且提高了零部件的跳动公差和焊接质量,省略掉了对材料卷100% 跳动检查以及压平材料卷的工序。在卷槽和耳轴盘之间非对准焊接非常少见,因此研磨和焊接修补步骤也被 完全去掉了。
“看了很多可替代的方法,例如管道和耳轴的加工以及卷的重新设计,但是这些方法长期来看会增加成本。”NewHolland 公司制造工艺和技术运营专家Bob Burkholder 说道。“同Motoman 公司合作,我们将现有的提供更好零部件质量、更节省成本的概念开发出来,我们最初的想法是可以得到实现的。”
在工作间里通过重力给料设备,管道进入机器人工作间内,同时耳轴通过Motoman公司MR-300 旋转定位器进入。两个固定装置每个包含有24 个耳轴。有效荷载为200kg(441 磅)、水平长度为2,651mm(104.4 英寸) 的6 轴HP200 机器人在工作间内进行处理工作。自定义手臂工具将一个管道和两个耳轴夹取。两个巨大的夹子同时抓住管道,同时两套较小的机器爪抓住两个耳轴。
“固定焊接设备以及机器人操作器上的自定心爪抓住耳轴和管道,这样零件的寿命差异显著减少。”负责机器人工作间的焊接/ 制造工程师Clint Hinkle说道。“这种方法保证了耳轴永远被插入到管道的中心,这样排除了材料和零部件的差异。”
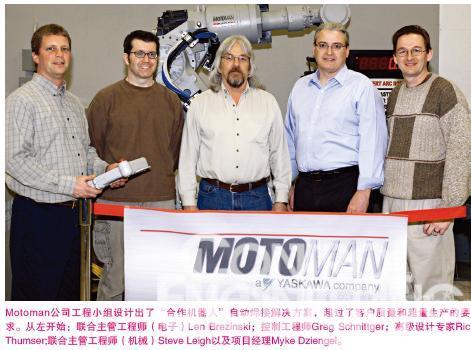
Motoman 公司应用工程师主管MykeDziengel 补充道, 项目最关键的因素是耳轴的寿命,而焊接质量是第二位。“工具给耳轴的排列提供了必要的保证,而水平焊接位置则保证了焊接质量。”Dziengel 说道。
电子工程师Len Brezinski 说道,对系统的精确度也很重要的是安装在夹子上的激光传感器。通过复杂的软件例常搜索,激光在管道表面探测出空洞和槽坑。然后旋转管道找寻空洞或者槽坑的位置,给出适合焊接的精确定位。为了消除任何由于槽坑或槽内灰尘导致的非对准焊接错误,传感器也会测量槽坑的位置。如果槽坑的大小不对,传感器就会运动到下一个槽坑。传感器还会根据位置、出现以及没出现的零部件细节核实零件的数量,以及管道的长度和直径。在装载到固定位置之间,位于监测站的另一个激光传感器会检查每个耳轴零件,以确定耳轴焊接轴的长度,以及它们和爪之间的位置。这些信息决定了装置的机械滑道将会把耳轴插入到每个管道内的深度。
终焊接操作。滑动装置与Yaskawa有着相同类型的伺服电机,都是由机器人控制器来控制机器人以及这些电机。滑动装置的两头可以闭合,允许HP500机器人进行焊接操作。一旦焊接结束了,HP200 机器人就可以往重力给料滑道内装载产品。转换零件模型非常简单,一般由其他机器人程序来进行选择。
控制和设计工具
在New Holland 公司的产品应用中,Motoman 公司的两个机器人都由NX100DR2C 机器人控制器来控制,这是一种单一程序独立控制器。New Holland 公司决定重新布置工作间,这种控制器的结构让工作间的布局更加灵活,可以让两个机器人和控制器分离开来。一个NX100控制器可以控制36 轴运动(多达4 个带独立程序的机器人)。
对于整体工作间控制来说,他们采用了带MotoHMI 用户界面的Allen-Bradley SLC 5/05 可编程逻辑控制器(PLC)。
Dziengel 说,在设计系统的软件工具方面,设计小组依靠Solid Edge 软件做
整体系统设计,然后依靠Soild EdgeFEA 软件工具对大多数关键区域的压力进行分析。他还补充道,MotoSim 软件可以帮助将两个机器人安置下来,并确定在工作间内的位置,因为零部件可能比较长(最终焊接部件大约最多有77 英寸长)。“机器人可达到区域大小非常关键。”Dziengel 说道。“对机器人的的放置偏差半英寸就会决定成败。”
项目成功也依靠New Holland 公司与Motoman 公司紧密合作,以及设计小组必要的各种工程学科技术支持。“有些小组成员之间就有焊接耳轴和管道的经验,还提供了不同的观点来满足设计需要。” Dziengel 说道。“与此同时,其他人提供用于计算焊接曲解经受压力的数学公式、机械爪的压力、框架以及滑动尺寸。”
质量的迅猛进步
最后,Motoman 公司设计的系统超出了New Holland 公司的质量革新要求。最终保持耳轴尺寸差异小于0.2mm(0.008 英寸),管道的差异小于0.75mm(0.030 英寸)。这个结果是比预期的项目成果好的多。高质量的零部件业降低了额外加工操作的需要以及相关的直接劳动力成本。
另外,新工作间超出了项目预期,能够实现无人生产监控一小时的目标。当车间采用了额外的工具和零部件革新技术后,原来5 到6 分钟完成一个产品的周期时间也得到改善。
“工作间在2007 年8 月底安装好,而且运行无大问题发生。”New Holland公司Hinkle 说道。“除了维护焊接枪以外,工作间日以继夜的工作,没有休息也没有午餐时间。工作间的成果是Motoman 以及New Holland 两家公司通力合作的结果。”